[Sharp HSS Blade for Machining Applications]Enhancing Precision and Efficiency in Machining Applications with Sharp HSS Blade: A Comprehensive Guide to Benefits and Selection
News 2024-10-4
In the intricate world of machining applications, the choice of tools significantly influences the quality of the finished product, production speed, and cost efficiency. Among various cutting tools available in the market, High-Speed Steel (HSS) blades stand out due to their exceptional hardness, durability, and adaptability in a range of machining environments. This article delves into the advantages of utilizing a sharp HSS blade in machining applications, the factors to consider when selecting one, and tips for maintaining them for optimal performance.
Understanding High-Speed Steel (HSS)
High-Speed Steel (HSS) is an alloy tool steel that is typically used for manufacturing cutting tools. It is designed to withstand high temperatures generated during machining, making it ideal for cutting tools like drills, taps, lathe tools, and blades. The high hardness and toughness of HSS allow it to retain its cutting edge even when subjected to severe operating conditions. This unique property is what makes a sharp HSS blade indispensable in various machining applications.
Benefits of Using Sharp HSS Blades
1. **Durability and Longevity**: One of the primary benefits of sharp HSS blades is their ability to maintain their edge much longer than other materials. This longevity reduces the frequency of tool replacement, leading to cost savings in manufacturing processes.
2. **High Cutting Speeds**: The sharpness of the HSS blade allows for higher cutting speeds without compromising on the quality of the finished product. This can significantly increase production rates, which is particularly beneficial in high-volume manufacturing scenarios.
3. **Versatility**: Sharp HSS blades can cut a variety of materials, including metals like steel, aluminum, and even some composites. Their adaptability makes them suitable for different machining applications, from turning and milling to drilling and planing.
4. **Quality of Finish**: The sharpness of the blade influences the surface finish of the machined part. A sharper blade produces cleaner cuts with minimal burrs or distortions, resulting in a better surface finish and reducing the need for additional machining processes.
5. **Heat Resistance**: HSS retains its hardness even at high temperatures, which allows for efficient machining without the risk of the tool softening. This feature is crucial when working with tougher materials that generate more heat during cutting.
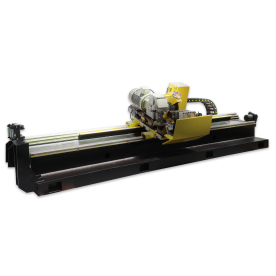
Enhancing Precision and Efficiency in Machining Applications with Sharp HSS Blade: A Comprehensive Guide to Benefits and Selection
When selecting a sharp HSS blade for machining applications, several factors should be taken into account to ensure optimal performance:
1. **Blade Geometry**: The design of the blade, including its shape and angle, affects cutting efficiency and the type of material it can effectively work with. A blade with a suitable geometry for specific machining tasks will yield better results.
2. **Coating Options**: While sharp HSS blades inherently possess great properties, applying a coating can enhance their performance even more. Coatings such as TiN (Titanium Nitride) reduce friction and wear, leading to longer tool life and improved surface finishes.
3. **Blade Size**: Depending on the machining task, the size of the HSS blade also impacts its effectiveness. Choosing the right size helps optimize cutting power and efficiency.
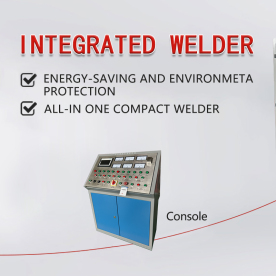
Enhancing Precision and Efficiency in Machining Applications with Sharp HSS Blade: A Comprehensive Guide to Benefits and Selection
Maintenance Tips for Sharp HSS Blades
To extend the life of sharp HSS blades and improve their cutting performance, follow these maintenance tips:
1. **Proper Storage**: Store blades in a dry, organized environment to avoid dulling from contact with other tools or elements. Using blade protectors can help maintain sharpness.
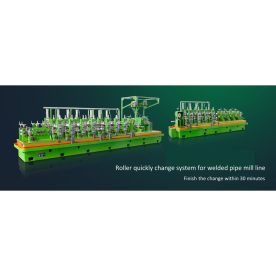
Enhancing Precision and Efficiency in Machining Applications with Sharp HSS Blade: A Comprehensive Guide to Benefits and Selection
3. **Cleaning and Lubrication**: After use, clean the blades to remove chips and debris. Additionally, use appropriate lubricants during machining to reduce friction and heat, further prolonging blade life.
4. **Check Alignment and Setup**: Ensure that the blades are properly aligned and set up in the machine to avoid unnecessary wear and tear, which can lead to premature dulling.
Conclusion
In summary, the sharp HSS blade is an essential component in machining applications, offering numerous benefits such as durability, versatility, and superior cutting performance. By carefully selecting the right blade and maintaining it properly, manufacturers can enhance efficiency, improve the quality of their products, and ultimately achieve cost savings in their operations. Investing time and resources into understanding and utilizing sharp HSS blades can yield significant returns in any machining environment.