[IF pipe seam annealing machine ]Revolutionizing Manufacturing Processes: The Integral Role of IF Pipe Seam Annealing Machines in Modern Industry
News 2024-10-4
****In the realm of modern manufacturing, technological advancements have continually played a vital role in improving efficiency, product quality, and operational capabilities. Among these advancements, the use of IF (Inductive Furnace) pipe seam annealing machines stands out as a critical innovation for industries involved in pipe manufacturing, particularly those producing welded pipes. These machines are designed to enhance the mechanical properties of pipes and, therefore, play a significant role in ensuring the overall integrity and reliability of the product.
What is IF Pipe Seam Annealing?
IF pipe seam annealing is a process that applies heat to the seams of welded pipes to relieve residual stresses, improve material properties, and prevent failures during service. The use of an inductive heating method allows for precise temperature control and rapid heating, making it an ideal choice for this application. This technology significantly contrasts with traditional heating methods, which often lead to uneven heating and longer processing times.
The Importance of Annealing in Pipe Manufacturing
The annealing process in pipe manufacturing is critical for several reasons. First and foremost, it eliminates the internal stresses that develop during welding. These stresses can be detrimental, leading to issues like warping, cracking, or even complete failure of the pipe under operational pressures. By employing an IF pipe seam annealing machine, manufacturers ensure that the pipes can withstand the rigors of their intended applications, whether in construction, oil and gas transport, or other industries.
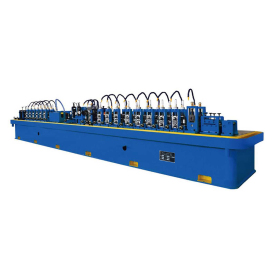
Revolutionizing Manufacturing Processes: The Integral Role of IF Pipe Seam Annealing Machines in Modern Industry
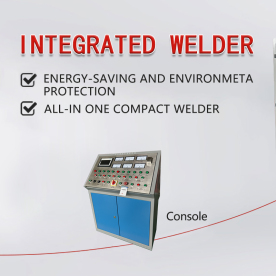
Revolutionizing Manufacturing Processes: The Integral Role of IF Pipe Seam Annealing Machines in Modern Industry
Features of IF Pipe Seam Annealing Machines
IF pipe seam annealing machines come equipped with several features that make them advantageous over traditional systems:
1. **Inductive Heating Technology**: This method of heating is energy-efficient and allows for rapid temperature changes, minimizing the time needed for the annealing process. The inductive coils generate heat directly in the pipe material, allowing for controlled and uniform heating.
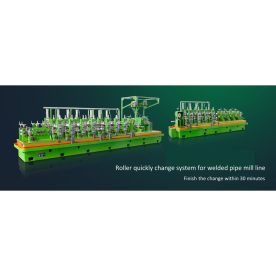
Revolutionizing Manufacturing Processes: The Integral Role of IF Pipe Seam Annealing Machines in Modern Industry
3. **Environmentally Friendly**: Traditional heating methods can involve significant energy consumption and emissions. In contrast, the inductive heating process is more efficient and generates less waste heat, making it more environmentally friendly.
4. **Versatility**: These machines can be used on various pipe sizes and materials, making them suitable for different manufacturing needs. This adaptability is crucial for manufacturers looking to diversify their product lines without investing in multiple machines.
Advantages of Using IF Pipe Seam Annealing Machines
Incorporating IF pipe seam annealing machines into a manufacturing operation provides numerous advantages. Firstly, the enhanced product quality reduces the rates of returns and failures, thereby improving customer satisfaction and trust in the product. Secondly, the efficiency gained through automated processes means that manufacturers can increase their output without compromising on quality.
Additionally, this technological advancement can result in significant cost savings. Reduced energy consumption, shorter processing times, and decreased risks of defective products all contribute to lowering operational costs. Manufacturers who adopt IF technology can expect to see a positive impact on their bottom line.
Conclusion
In conclusion, IF pipe seam annealing machines are revolutionizing the manufacturing processes within the pipe production industry. Their ability to enhance product quality, improve safety, and increase efficiency has made them an indispensable asset for manufacturers. As industries continue to evolve, embracing such advanced technologies will be essential for maintaining competitive advantages and meeting ever-increasing consumer expectations. The future of pipe manufacturing looks bright with the integration of IF pipe seam annealing machines leading the way in quality and innovation.
By understanding the integral role that these machines play, manufacturers can better position themselves to take advantage of the benefits they offer, ensuring resilience and reliability in their product offerings.