[High frequency welder equipment]Exploring the Benefits and Applications of High Frequency Welder Equipment in Modern Manufacturing Processes
News 2024-10-4
In today’s rapidly advancing industrial landscape, manufacturers are continuously seeking ways to enhance productivity and improve the quality of their products. One technological innovation that has gained significant traction is high frequency welder equipment. This specialized welding technology is known for its efficiency, precision, and versatility across a variety of applications. In this article, we will explore what high frequency welding is, its benefits, applications in different industries, and considerations for manufacturers looking to integrate this technology into their operations.
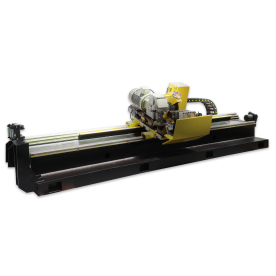
Exploring the Benefits and Applications of High Frequency Welder Equipment in Modern Manufacturing Processes
High frequency welding is a process that uses high-frequency electrical currents to generate heat, which is then used to join materials together. The welding occurs rapidly, making it suitable for continuous production processes. This method is particularly effective for joining thermoplastic materials and even some metals through its unique ability to penetrate the materials deeply, providing strong and durable welds.
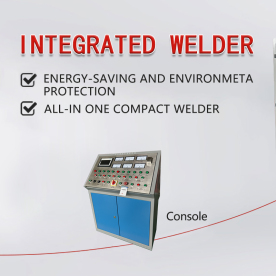
Exploring the Benefits and Applications of High Frequency Welder Equipment in Modern Manufacturing Processes
Benefits of High Frequency Welder Equipment
The benefits of using high frequency welder equipment in manufacturing are manifold:
1. **Speed and Efficiency:** High frequency welding processes are significantly faster compared to traditional welding methods. This speed enables manufacturers to streamline their production lines and meet tight deadlines, increasing overall efficiency.
2. **Quality of Welds:** The precision of high frequency welding leads to consistent and high-quality welds. This is particularly important in industries such as automotive and aerospace, where weld integrity is critical for safety and performance.
3. **Energy Efficiency:** High frequency welding equipment tends to be more energy-efficient than other welding processes. This reduces operational costs and aligns with sustainability goals that many companies strive to achieve.
4. **Versatility:** High frequency welders can work with various materials, including plastics, rubber, and certain metals. This flexibility allows manufacturers to utilize a single piece of equipment for multiple applications, reducing capital expenditure on specialized machines.
5. **Environmentally Friendly:** High frequency welding generally produces less waste compared to traditional welding methods, as it often requires fewer consumables and generates less thermal distortion. This environmentally conscious approach is becoming increasingly important for compliance with regulations and corporate responsibility initiatives.
Applications of High Frequency Welder Equipment
High frequency welding finds applications in diverse industries, each leveraging its unique advantages:
1. **Automotive Industry:** In the automotive sector, high frequency welding is used to create complex geometries in plastic components, bumpers, and interior parts. The ability to achieve strong and consistent welds is crucial for safety and performance.
2. **Textile and Fabric Welding:** High frequency welding is widely used in the production of water-resistant textiles, banners, and tarps. The process allows for seamless joining of fabrics without the use of thread, enhancing durability and aesthetics.
3. **Packaging Industry:** In packaging, high frequency welders are employed to create airtight seals in plastic pouches and containers. This ensures product freshness and safety while extending shelf life.
4. **Medical Device Manufacturing:** The medical industry benefits from high frequency welding for producing sterile packaging and joining components of medical devices where precision and cleanliness are paramount.
Considerations for Manufacturers
While integrating high frequency welder equipment can lead to significant advantages, manufacturers should consider several factors:
- **Investment Costs:** High frequency welding equipment can be a substantial initial investment. Manufacturers should evaluate their production needs to ensure a return on investment over time.
- **Training and Expertise:** Proper training is essential for staff operating high frequency welding equipment. Understanding the nuances of the technology will maximize efficiency and product quality.
- **Equipment Maintenance:** Like any technological equipment, high frequency welders require regular maintenance to ensure optimal performance. Establishing a maintenance routine can prevent costly downtime.
Conclusion
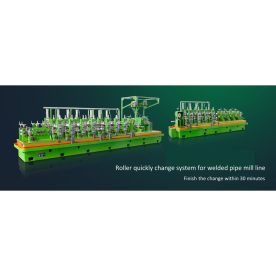