[Customized pipe mill production line solutions]Innovative Customized Pipe Mill Production Line Solutions: Tailoring Manufacturing to Meet Diverse Industry Needs and Boost Efficiency
News 2024-10-3
****In today's competitive manufacturing landscape, companies are increasingly seeking solutions that not only enhance productivity but also provide flexibility in their operations. Customized pipe mill production line solutions represent a significant advancement in the steel and pipe manufacturing industry, allowing manufacturers to meet specific demands while streamlining their processes. This article delves into the importance of tailored pipe mill systems, the benefits they offer, and considerations for implementing such solutions in various industrial applications.
Understanding Customized Pipe Mill Production Lines
A pipe mill production line is a series of interconnected machinery and processes designed for the manufacture of pipes out of steel or other materials. Traditional pipe mills often operate on a one-size-fits-all model, leading to inefficiencies, wasted materials, and limited adaptability to market changes. Customized pipe mill production line solutions address these limitations by creating configurations that are specifically designed for the unique requirements of each manufacturer.
Customization can involve various factors, such as pipe diameter, wall thickness, material type, production speed, and the addition of secondary processing capabilities. With advancements in technology, manufacturers now have the opportunity to create sophisticated production lines that cater to diverse specifications while ensuring high-quality output.
Benefits of Customized Pipe Mill Production Lines
1. **Increased Efficiency**: Customized production lines are designed to minimize downtime and optimize workflow. By tailoring each component to suit specific production needs, manufacturers can achieve faster cycle times and reduce the likelihood of errors that can lead to costly rework.
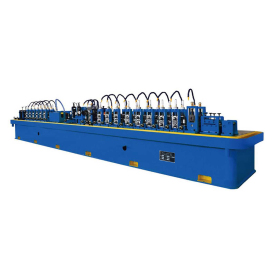
Innovative Customized Pipe Mill Production Line Solutions: Tailoring Manufacturing to Meet Diverse Industry Needs and Boost Efficiency
3. **Enhanced Quality Control**: Customization extends to quality assurance processes as well. Manufacturers can implement advanced inspection and testing protocols within the production line, ensuring that each pipe meets stringent industry standards. This is particularly essential for industries where safety and reliability are paramount, such as construction, energy, and transportation.
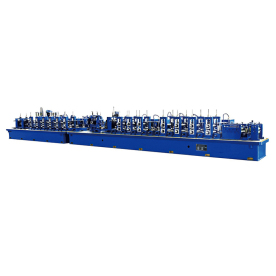
Innovative Customized Pipe Mill Production Line Solutions: Tailoring Manufacturing to Meet Diverse Industry Needs and Boost Efficiency
5. **Integration of Technologies**: Customized solutions can incorporate the latest manufacturing technologies, such as automation, robotics, and advanced data analytics. This integration can lead to improved operational efficiency and the ability to monitor production in real-time, further enhancing decision-making capabilities.
Key Considerations for Implementing Customized Solutions
While the benefits of customized pipe mill production lines are clear, implementing such solutions requires careful consideration:
1. **Needs Assessment**: Before embarking on the customization journey, manufacturers should conduct a thorough analysis of their specific needs and goals. This may include reviewing current production capabilities, market trends, and potential areas for improvement.
2. **Collaboration with Experts**: Partnering with machinery manufacturers and industry experts is crucial for developing effective customized solutions. These partnerships can provide valuable insights into the latest technologies and best practices, ensuring that the production line design aligns with both current and future manufacturing trends.
3. **Scalability**: As market demands fluctuate, manufacturers must consider the scalability of their customized production lines. Systems should be designed not only to meet current needs but also to accommodate potential growth and diversification in the future.
4. **Training and Support**: Employees will require training on the new systems and processes introduced by the customized production lines. Comprehensive training programs should be established to ensure that the workforce is adept at operating the new machinery and maintaining quality control.
Conclusion
