[All-in-one High Frequency Welder for Metal Processing]Revolutionizing Metal Processing: The All-in-One High Frequency Welder for Efficient and Versatile Fabrication Solutions
News 2024-10-3
In the modern landscape of manufacturing and metalworking, the demand for advanced and efficient techniques has never been higher. As industries evolve, so does the technology that drives them, and one of the standout innovations is the All-in-One High Frequency Welder. This sophisticated piece of equipment not only fulfills a range of welding needs but also offers unparalleled efficiency, precision, and versatility in metal processing.
High frequency welding, a method that uses electromagnetic energy, has gained recognition for its ability to create strong, consistent welds in a variety of metal types, including aluminum, stainless steel, and copper. The All-in-One High Frequency Welder streamlines the process by integrating multiple functionalities into one compact unit. This means fabricators no longer need to invest in separate welding machines for different applications, drastically reducing costs and operational complexity.
Unmatched Versatility
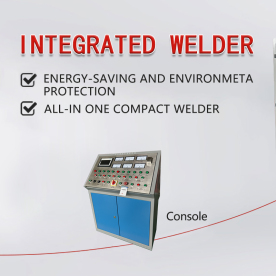
Revolutionizing Metal Processing: The All-in-One High Frequency Welder for Efficient and Versatile Fabrication Solutions
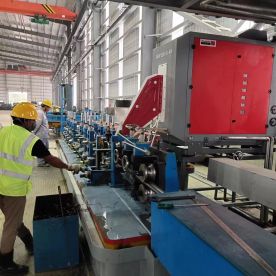
Revolutionizing Metal Processing: The All-in-One High Frequency Welder for Efficient and Versatile Fabrication Solutions
Enhanced Efficiency and Productivity
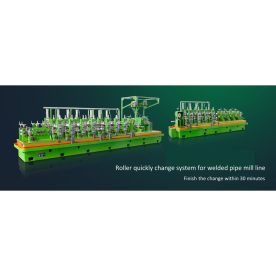
Revolutionizing Metal Processing: The All-in-One High Frequency Welder for Efficient and Versatile Fabrication Solutions
Moreover, the compact design of the welder makes it easy to set up and configure, which helps to minimize downtime. In an industry where time is money, being able to streamline the welding process results in significant financial savings and enhanced productivity. With its advanced digital controls and user-friendly interface, operators can easily manage settings and monitor the welding process in real-time, further boosting efficiency.
Improved Quality of Welds
When it comes to welding, the quality of the weld joint is paramount. The All-in-One High Frequency Welder ensures superior weld quality through its precise control over heat and pressure. This leads to stronger bonds and reduces the likelihood of defects, such as porosity, that can compromise the structural integrity of the finished product.
In addition, the welder's ability to operate at high frequencies allows for rapid heating, which minimizes the heat-affected zone (HAZ) and preserves the properties of the base metal. As a result, final products exhibit excellent mechanical properties, making them more reliable in their intended applications.
Conclusion
As industries continue to seek innovative solutions to improve their manufacturing processes, the All-in-One High Frequency Welder is poised to lead the charge in metal processing technology. By combining versatility, efficiency, and quality, this equipment not only meets the diverse needs of modern metal fabrication but also sets a new standard for what is possible in welding.
Investing in an All-in-One High Frequency Welder can ultimately transform a business’s capabilities, contributing to increased output and improved product quality. As the landscape of metal processing continues to evolve, adopting cutting-edge technology like this welder will be essential for companies aiming to stay ahead of the competition and meet the demands of the future.