[Solid state HF welder with wire feed system]Revolutionizing Metal Joining: The Advantages of Solid State HF Welder with Wire Feed System in Modern Manufacturing
News 2024-10-3
****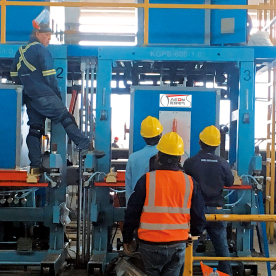
Revolutionizing Metal Joining: The Advantages of Solid State HF Welder with Wire Feed System in Modern Manufacturing
Understanding Solid State HF Welding
Solid state HF welding is a process that utilizes high-frequency electrical energy to create heat in the workpieces that are being joined. Unlike traditional welding methods, which often rely on consumable electrodes or high-temperature gas flames, solid state HF welding uses electromagnetic fields to induce resistance heating in metal components. This process allows for rapid heating and cooling, resulting in strong and durable welds while minimizing distortion and thermal stress.
The addition of a wire feed system to the solid state HF welder enhances its capabilities significantly. The wire feed mechanism supplies consumable filler material directly to the weld zone, allowing for improved control and consistency in the welding process. This is especially beneficial when the thickness of the metal components varies, or when additional material is required to fill gaps in the joint.
Advantages of Solid State HF Welders with Wire Feed Systems
1. **Precision and Control**: Solid state HF welders with wire feed systems provide excellent control over the welding parameters. Operators can adjust variables such as feed rate, voltage, and welding speed in real-time, resulting in welds that meet stringent quality standards. Precise control allows manufacturers to achieve consistent results across multiple welds, reducing rework and scrap rates.
2. **High Speed and Efficiency**: The solid state nature of the HF welder enables rapid heating, which significantly reduces the overall welding time. Coupled with the wire feed system, the process can be completed more quickly than traditional welding methods. This enhanced speed helps manufacturers boost productivity, allowing them to meet evolving customer demands and improve their bottom line.
3. **Minimal Heat Affected Zone**: One of the significant advantages of solid state HF welding is the creation of a minimal heat affected zone (HAZ). This characteristic is essential in preserving the mechanical properties of the base metals. The localized heating ensures that the surrounding area remains cooler, which prevents warping, residual stress, and changes in the microstructure of the joints.
4. **Versatility**: Solid state HF welders with wire feed systems can work with various materials and thicknesses. This versatility makes them suitable for multiple applications, from joining thin sheet metal in automotive manufacturing to welding thicker components in industrial machinery. The ability to adapt to different materials ensures that manufacturers can use the same system for diverse products, reducing the need for specialized equipment.
5. **Reduced Consumable Costs**: The wire feed system allows for the use of consumable filler materials efficiently, enabling manufacturers to minimize waste. By controlling the amount of filler material fed into the weld, companies can optimize their resources and reduce overall costs associated with consumables.
6. **Safety Features**: Modern solid state HF welders are equipped with advanced safety features that protect operators from potential hazards. These machines often come with automatic shut-off systems, overload protection, and user-friendly interfaces, ensuring safe operation in complex manufacturing environments.
Applications in Modern Manufacturing
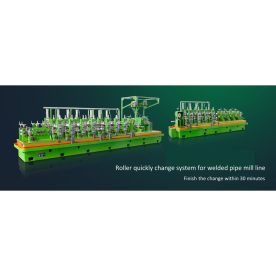
Revolutionizing Metal Joining: The Advantages of Solid State HF Welder with Wire Feed System in Modern Manufacturing

Revolutionizing Metal Joining: The Advantages of Solid State HF Welder with Wire Feed System in Modern Manufacturing
Conclusion
The solid state HF welder with wire feed system represents a significant advancement in welding technology, offering advantages in precision, efficiency, and adaptability for modern manufacturing processes. As industries continue to seek ways to enhance productivity while maintaining quality standards, this innovative welding method is poised to play a crucial role in the evolution of metal joining techniques. By integrating solid state HF welders into their operations, manufacturers can achieve superior results and stay competitive in an increasingly demanding market.