[Custom-Made Spare Parts for Solid State HF Welders]Harnessing Innovation: The Importance of Custom-Made Spare Parts for Solid State HF Welders in Modern Manufacturing
News 2024-10-2
In an era where precision and efficiency are paramount, the manufacturing industry continually seeks innovative solutions to improve production processes. One such advancement is the use of solid state HF (High Frequency) welders, which have revolutionized the welding landscape due to their reliability and capability to produce high-quality welds in various materials. However, like any sophisticated machinery, solid state HF welders are susceptible to wear and tear, requiring spare parts to maintain optimal performance. This article explores the significance of custom-made spare parts for solid state HF welders and why they are essential for uninterrupted operations and cost efficiency.
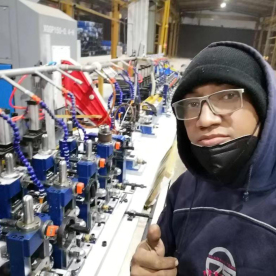
Harnessing Innovation: The Importance of Custom-Made Spare Parts for Solid State HF Welders in Modern Manufacturing
Solid state HF welders utilize advanced semiconductor devices instead of traditional vacuum tubes to generate high-frequency electrical energy. This technology offers several advantages, including a cooler operating temperature, improved reliability, and reduced energy consumption. They are widely used across various industries, including automotive, aerospace, and electronics, for applications like welding plastics, metals, and even joining dissimilar materials.
Despite their advanced technology, solid state HF welders can face various issues due to prolonged use, such as component fatigue, electrical failures, and wear on mechanical parts. Ensuring that these machines continue to operate at their best requires readily available spare parts. However, generic or stock replacement parts may not always fit perfectly or may compromise the efficiency of the welder, leading to potential operational delays or failures.
The Necessity of Custom-Made Spare Parts
Custom-made spare parts serve as a crucial lifeline for solid state HF welders. One size does not fit all in manufacturing machinery, and using custom components ensures compatibility, durability, and performance consistency. Here are several reasons why investing in custom-made spare parts is important:
1. **Precision Fit**: Custom parts are designed specifically for the machine’s unique specifications. This precision decreases the likelihood of malfunctions or inefficiencies that can arise from using ill-fitting parts.
2. **Enhanced Performance**: Tailoring spare parts to the exact needs of the welder can lead to improved performance. Custom parts can optimize the welding process, ensuring that high-quality welds are achieved consistently.
3. **Increased Lifespan**: Components manufactured to meet the original specifications can enhance the overall longevity of the welder. By utilizing the right materials and design, custom parts can resist wear and tear better than standard alternatives.
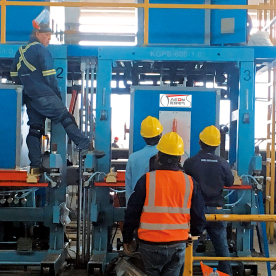
Harnessing Innovation: The Importance of Custom-Made Spare Parts for Solid State HF Welders in Modern Manufacturing
5. **Cost-Efficiency**: While there may be an initial investment in custom parts, the long-term benefits often outweigh these costs. Increased efficiency and reduced downtime lead to substantial savings over time, improving the overall return on investment.
6. **Innovative Solutions**: Collaborating with manufacturers to design custom parts can pave the way for innovative solutions that enhance the functionality of the existing machinery. This innovation can lead to new capabilities, which can be a competitive advantage in the market.
The Process of Creating Custom Parts
The creation of custom-made spare parts begins with precise analysis. Engineers assess the specific requirements of the welder, acknowledging the parts' dimensions, material properties, and performance needs. Advanced technologies such as Computer-Aided Design (CAD) and 3D printing are often utilized to develop prototypes, allowing for quick iterations and refinements.
Once the design is finalized, manufacturing might involve various processes, including CNC machining, injection molding, or additive manufacturing, depending on the complexity and material requirements. Finally, rigorous quality control ensures that parts meet the necessary standards for functionality and safety.
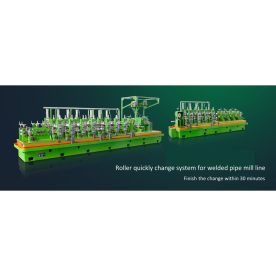
Harnessing Innovation: The Importance of Custom-Made Spare Parts for Solid State HF Welders in Modern Manufacturing
In conclusion, the importance of custom-made spare parts for solid state HF welders cannot be overstated. As industries strive for greater efficiency and quality control, having the right components is essential to maintaining a seamless production process. By investing in custom-made solutions, manufacturers can enjoy enhanced performance, longevity, and overall operational success in their welding applications. As the industry evolves, embracing the benefits of custom components will be key to staying competitive and fulfilling the demands of modern manufacturing.