[Solid state high frequency welder machine]The Revolutionary Impact of Solid State High Frequency Welder Machines on Modern Manufacturing Processes
News 2024-10-1
In today's fast-paced industrial landscape, efficiency, precision, and reliability are paramount. As manufacturers strive to elevate their production capabilities, the importance of innovative technologies cannot be overstated. One such innovation making significant waves in the manufacturing sector is the solid state high frequency welder machine. This sophisticated machinery is revolutionizing the way metal components are joined together, setting new standards in quality and efficiency.
The solid state high frequency welder machine utilizes advanced semiconductor technology to deliver stable and precise welding operations. Unlike traditional welding machines that rely on vacuum tubes, solid state technology provides several advantages that enhance the welding process. These machines operate at high frequencies, allowing for faster welding speeds and significantly reduced cycle times. This efficiency is particularly crucial for industries that require high-volume production, such as automotive manufacturing, electronics, and heavy machinery.
One of the standout features of solid state high frequency welders is their ability to maintain consistent power outputs. This is achieved through digital control systems that monitor and adjust the welding parameters in real time. As a result, manufacturers benefit from improved weld quality, as the consistent heat and pressure applied during the welding process lead to stronger joints with fewer defects. This increased reliability reduces waste and rework, ultimately contributing to higher profitability and less environmental impact.
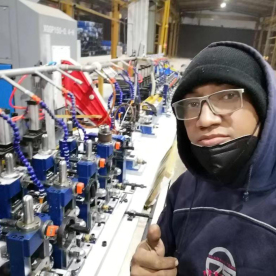
The Revolutionary Impact of Solid State High Frequency Welder Machines on Modern Manufacturing Processes
The versatility of solid state high frequency welders also plays a critical role in their growing popularity. They are capable of welding a wide array of materials, including ferrous and non-ferrous metals, plastics, and even composite materials. This capability makes them particularly valuable in diverse industries where different materials need to be joined quickly and effectively. Furthermore, their ability to handle thin gauges of materials reduces the risk of warping or distortion, which is often a concern with traditional welding methods.
In terms of energy efficiency, solid state high frequency welder machines also stand out. Their design allows for lower energy consumption during operation, which not only contributes to cost savings but also aligns with the increasingly important goal of sustainable manufacturing practices. Higher energy efficiency translates to reduced carbon emissions and a lower overall environmental footprint, making them an attractive option for companies looking to enhance their green credentials.
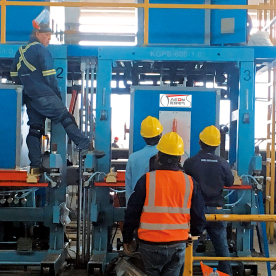
The Revolutionary Impact of Solid State High Frequency Welder Machines on Modern Manufacturing Processes
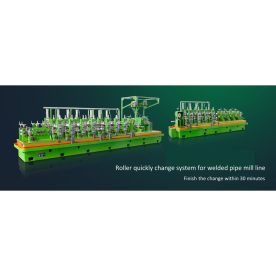
The Revolutionary Impact of Solid State High Frequency Welder Machines on Modern Manufacturing Processes
As industries continue to evolve, the adoption of technologies like the solid state high frequency welder machine will become even more essential for businesses aiming to maintain a competitive edge. The combination of enhanced welding precision, improved cycle times, and reduced environmental impact positions these machines as a cornerstone of modern manufacturing processes.
In conclusion, the solid state high frequency welder machine is not just a technological advancement; it represents a transformation in the way manufacturers approach welding and assembly. As the push for higher productivity, lower costs, and sustainable practices intensifies, forward-thinking industries will increasingly rely on this cutting-edge equipment to meet their objectives. The future of welding is undoubtedly bright, with solid state technology leading the charge into a new era of manufacturing excellence.