[Industrial induction heating equipment]Exploring the Advantages and Applications of Industrial Induction Heating Equipment in Modern Manufacturing Processes
News 2024-9-30
****Industrial induction heating equipment has emerged as a revolutionary approach in the manufacturing sector, transforming the way industries process metals and other conductive materials. This technology harnesses the principles of electromagnetism to elevate temperatures efficiently, providing numerous benefits over traditional heating methods. Whether in automotive, aerospace, or general manufacturing, the versatility and effectiveness of induction heating offer significant advantages that cannot be overlooked. In this article, we will delve into the mechanics of induction heating, its numerous applications, and the reasons why this technology is becoming increasingly indispensable in various industries.
At its core, induction heating relies on the principle of electromagnetic induction. When an alternating current flows through a coil, it creates a magnetic field that penetrates conductive materials placed within or near the field. This magnetic field induces electrical currents, known as eddy currents, within the material, which generate heat due to the material’s resistance to the electrical flow. This heat can be precisely controlled by adjusting the power input and the frequency of the electromagnetic field, making induction heating a highly efficient method for temperature regulation.
One of the most notable advantages of industrial induction heating equipment is its efficiency. Conventional heating methods, such as furnaces or gas burners, typically involve heating the ambient environment and relying on conduction or convection to transfer that heat to the workpiece. This method is not only less efficient but also often results in significant energy loss. In contrast, induction heating directly targets the material, leading to rapid heating times, reduced energy consumption, and lower operational costs. Studies have shown that induction heating can be up to 90% efficient, compared to only 40-50% for traditional methods.
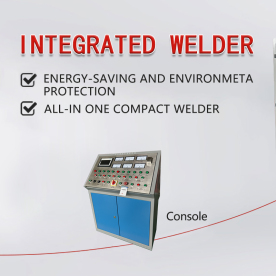
Exploring the Advantages and Applications of Industrial Induction Heating Equipment in Modern Manufacturing Processes
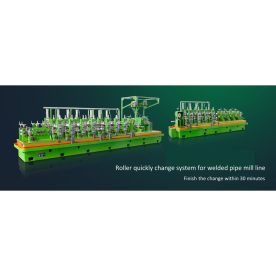
Exploring the Advantages and Applications of Industrial Induction Heating Equipment in Modern Manufacturing Processes

Exploring the Advantages and Applications of Industrial Induction Heating Equipment in Modern Manufacturing Processes
Another significant application is in the realm of metal joining and brazing. The induction heating process allows for the fast and clean joining of metals, which is crucial in applications requiring high-strength connections without compromising surrounding materials. This is particularly useful in industries where precision is paramount, such as electronics and medical devices.
Additionally, induction heating equipment is invaluable in the field of plastics processing and polymer curing. Induction technology can be utilized to achieve rapid heating of mold and tooling, ensuring that production cycles are significantly reduced. This translates to increased productivity and reduced time-to-market for various consumer products.
Safety is another area where industrial induction heating equipment excels. Traditional heating methods often pose risks due to open flames and high-temperature surfaces, leading to hazards such as burns and fire. In contrast, induction heating systems operate at lower surface temperatures, significantly reducing the risk of accidents. The equipment also often includes advanced safety controls, further ensuring a safer work environment.
As industries continue to evolve, the demand for energy-efficient, precise, and versatile heating solutions will only increase. Industrial induction heating equipment stands out as a key technology that aligns with these trends, offering benefits that traditional methods cannot match. Therefore, investing in induction heating can be a strategic move for businesses looking to enhance their manufacturing processes, improve product quality, and maintain a competitive edge in the ever-evolving industrial landscape.
In conclusion, industrial induction heating equipment represents a significant advancement in the manufacturing sector. Its efficiency, precision, safety, and range of applications make it a critical tool for modern industries aiming for excellence. As technology continues to advance, we can anticipate even further innovations in induction heating that will drive productivity and quality across various sectors.