[High-efficiency ERW tube mill]Maximizing Production with High-Efficiency ERW Tube Mills: The Future of Seamless Steel Pipe Manufacturing
News 2024-9-30
In the ever-evolving landscape of manufacturing, particularly in the metalworking sector, the demand for efficiency and quality has never been more pronounced. This trend is especially significant in the production of steel pipes and tubes, where manufacturers are continually seeking ways to optimize their operations. One technological advancement that stands out is the High-efficiency ERW (Electric Resistance Welding) Tube Mill. This innovative equipment not only enhances productivity but also improves the quality of the end product, making it essential for modern manufacturing processes.
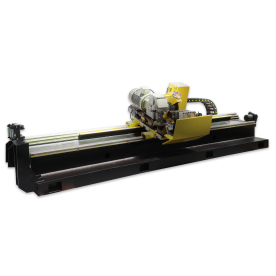
Maximizing Production with High-Efficiency ERW Tube Mills: The Future of Seamless Steel Pipe Manufacturing
One of the key benefits of high-efficiency ERW tube mills is their ability to operate at significantly higher speeds than conventional tube mills. Traditional models may produce tubes at rates of 40 to 60 meters per minute; however, high-efficiency variants can achieve speeds exceeding 100 meters per minute. This increase in production speed directly translates to higher output and reduced labor costs, enabling manufacturers to meet the growing demand for steel tubes in various industries, such as construction, automotive, and oil and gas.
Another significant advantage of these advanced tube mills lies in their versatility. High-efficiency ERW tube mills can accommodate different steel grades and various tube sizes, making them suitable for a wide range of applications. Whether manufacturing structural tubes, precision tubing, or large-diameter pipes, these mills can easily switch between production runs, which is crucial in today's market, where customization and rapid turnaround times are in high demand.
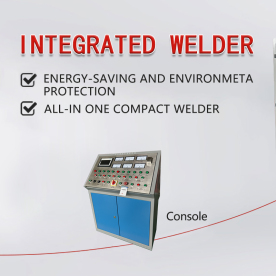
Maximizing Production with High-Efficiency ERW Tube Mills: The Future of Seamless Steel Pipe Manufacturing
Moreover, energy efficiency is a growing concern in manufacturing, and high-efficiency ERW tube mills address this issue head-on. With advanced energy-saving features, such as variable frequency drives and efficient cooling systems, these mills consume significantly less energy compared to older models. This not only lowers operating costs but also aligns with the increasing need for environmentally sustainable manufacturing practices, helping companies meet regulatory requirements and improve their public image.
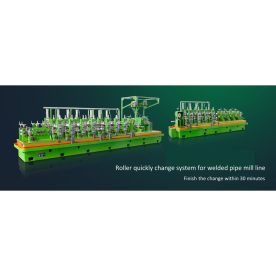
Maximizing Production with High-Efficiency ERW Tube Mills: The Future of Seamless Steel Pipe Manufacturing
In conclusion, the High-efficiency ERW tube mill represents a pivotal advancement in the steel pipe manufacturing industry. By maximizing production speed, enhancing quality control, increasing versatility, and promoting energy efficiency, these mills are redefining manufacturing standards. As the demands of the market evolve, manufacturers who invest in high-efficiency ERW tube mills will undoubtedly position themselves for sustained success in an increasingly competitive landscape. Embracing these cutting-edge technologies not only prepares manufacturers for current needs but also equips them to tackle future challenges head-on, ensuring their relevance in the dynamic world of manufacturing.