[Portable high frequency welder]Exploring the Benefits and Applications of Portable High Frequency Welder Technology in Modern Manufacturing and Repair Industries
News 2024-9-29
In today's fast-paced manufacturing and repair industries, the demand for efficient and effective welding solutions continues to grow. One technology that has gained significant traction is the portable high frequency welder. This innovative tool has revolutionized the way welding is approached across diverse applications, offering unmatched convenience and precision. In this article, we will explore the benefits, applications, and advancements associated with portable high frequency welders.
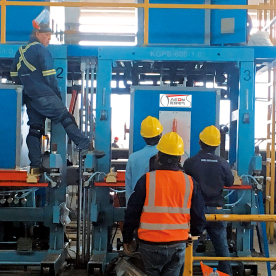
Exploring the Benefits and Applications of Portable High Frequency Welder Technology in Modern Manufacturing and Repair Industries
A portable high frequency welder is a compact welding machine that utilizes high-frequency electromagnetic fields to create strong welds in various materials. These welders are especially effective for joining thin materials, making them ideal for applications in industries ranging from automotive to aerospace. The portable nature of these welders allows for easy transport and setup, making them invaluable in fieldwork or areas with limited space.
Key Advantages of Portable High Frequency Welders
1. **Mobility and Convenience**: One of the most significant benefits of portable high frequency welders is their mobility. Unlike traditional welding machines, portable welders are lightweight and compact, designed for easy transport. This makes them perfect for on-site jobs where moving heavy equipment is impractical. Welders can quickly set up their equipment at various job sites, increasing operational efficiency.
2. **High Precision and Control**: Portable high frequency welders excel in delivering precise welds, which is essential in industries where quality cannot be compromised. The ability to control heat input and adjust frequencies allows welders to work on delicate materials without causing distortion or damage. This level of control is particularly advantageous in applications involving electronics or automotive components, where precision is crucial.
3. **Energy Efficiency**: These welders are designed to consume less power compared to traditional welding machines. By utilizing high-frequency technology, they can complete welding tasks more quickly and effectively, leading to increased energy savings. This aspect not only lowers operational costs but also reduces the environmental impact, aligning with the growing emphasis on sustainability in manufacturing.
4. **Versatile Applications**: Portable high frequency welders can be used to weld a wide variety of materials, including metals and plastics, making them highly versatile. Industries such as aviation, automotive, medical device manufacturing, and construction frequently utilize these welders. Whether fabricating components or performing repairs, the adaptability of portable high frequency welders plays a crucial role in enhancing productivity across sectors.
5. **Ease of Use**: Modern portable high frequency welders often come equipped with user-friendly interfaces that simplify operation. Many models feature digital displays and preset programs, allowing less experienced welders to achieve quality results without extensive training. The streamlined operation enables companies to minimize downtime and maximize the skills of their workforce.
Applications Across Industries
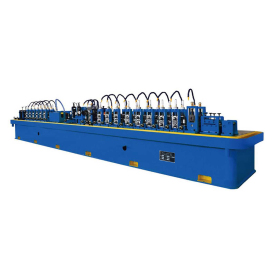
Exploring the Benefits and Applications of Portable High Frequency Welder Technology in Modern Manufacturing and Repair Industries
Aerospace is another sector benefitting from portable high frequency welding technology. The lightweight and compact design of these welders allows for quick repairs and assembly of aircraft components. Similarly, in the medical field, where precision is vital, portable welders are used in the manufacturing of surgical instruments and devices, ensuring that they meet stringent safety and quality requirements.
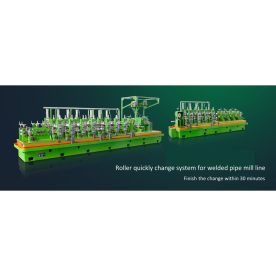
Exploring the Benefits and Applications of Portable High Frequency Welder Technology in Modern Manufacturing and Repair Industries
Conclusion
The introduction of portable high frequency welders has undoubtedly transformed the landscape of welding in modern manufacturing and repair industries. Their mobility, precision, energy efficiency, and versatility make them an appealing choice for a range of applications. As technology continues to advance, we can expect further enhancements in the performance and reliability of these welding machines, solidifying their place as essential tools in the welding industry. By embracing portable high frequency welders, businesses can not only enhance their operational efficiency but also ensure the delivery of high-quality products that meet the demands of today’s fast-paced markets.