[Customized Mould for Tube Mill Components]Unlocking Efficiency in Tube Manufacturing: The Importance of Customized Mould for Tube Mill Components
News 2024-9-28
****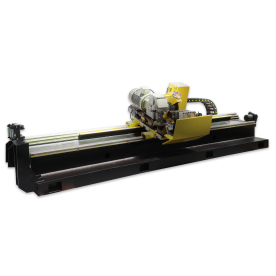
Unlocking Efficiency in Tube Manufacturing: The Importance of Customized Mould for Tube Mill Components
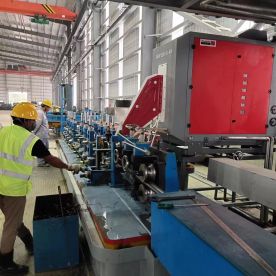
Unlocking Efficiency in Tube Manufacturing: The Importance of Customized Mould for Tube Mill Components
Tube mills are machines designed to shape raw metal into tubes or pipes through a series of rolls and forming steps. These mills typically operate with precision, as any flaw in the process can lead to substantial material waste and increased costs. Manufacturers are consistently on the lookout for ways to minimize production downtime, enhance product uniformity, and optimize the performance of their machines. Here, the significance of customized moulds becomes evident.
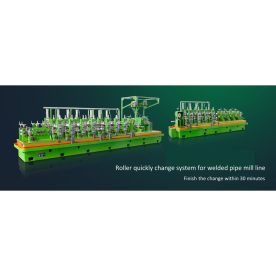
Unlocking Efficiency in Tube Manufacturing: The Importance of Customized Mould for Tube Mill Components
1. **Enhancing Precision and Quality**: Customized moulds are designed specifically to cater to the unique requirements of each tube mill and its product line. As every project has its specifications and characteristics, off-the-shelf moulds often fall short. Tailoring the design of moulds allows manufacturers to achieve a high level of precision, ensuring that the dimensions and tolerances of the end product meet rigorous standards. This precision is crucial in applications where safety and reliability are paramount, such as in the automotive and aerospace industries.
2. **Increasing Efficiency**: By employing customized moulds, tube mills can operate more efficiently. Moulds designed to fit perfectly with the machinery minimize the risk of misalignment and jamming. This translates to reduced downtime, as machines can run for longer periods without interruptions. Moreover, efficient moulds can contribute to faster production cycles, enabling manufacturers to fulfill orders more swiftly and handle larger volumes.
3. **Material Optimization**: Customized moulds can also help in optimizing the amount of raw material used. By ensuring a precise fit and shape in the manufacturing process, companies can minimize excess material that might otherwise go to waste. This not only reduces costs but also aligns with sustainable manufacturing practices, as it lessens the environmental impact by cutting down on waste.
4. **Adaptability to Market Changes**: Industries are continually evolving, with changing demands and requirements. Customized moulds can be modified and re-engineered in response to market trends. This adaptability allows manufacturers to pivot and introduce new products or modify existing designs without requiring an entirely new setup. As a result, businesses can stay competitive by quickly addressing shifts in consumer preferences.
5. **Cost Effectiveness in the Long Run**: Although the initial investment in customized moulds may be higher than standard options, the long-term benefits far outweigh these costs. The reduction in waste, increased machine uptime, and enhanced product quality lead to significant savings over time. Furthermore, the longevity and durability of well-designed moulds can reduce the frequency of replacements, contributing to a more cost-effective manufacturing process.
Conclusion
Customizing moulds for tube mill components is not just a trend; it is a necessary step in advancing manufacturing efficiency and product quality. As industries continue to face rising costs and competitive pressures, investing in tailored solutions becomes essential. Customized moulds enhance precision, improve efficiency, facilitate material optimization, promote adaptability, and drive long-term cost effectiveness.
In a landscape where speed, quality, and adaptability are crucial, embracing customized moulds can set a manufacturer apart from its competitors. Whether in automotive, aerospace, or any other industry relying on tube mill production, the benefits of using customized moulds are clear. As the future unfolds, those manufacturers who prioritize tailored solutions will likely lead the way in innovation and operational excellence, paving the path for sustainable growth in manufacturing.