[Solid state HF welder with temperature control]Exploring the Advantages and Applications of Solid State HF Welder with Temperature Control in Modern Manufacturing Processes
News 2024-9-27
In today's fast-paced manufacturing environment, precision and quality are paramount. One technology that has made significant strides in enhancing these aspects is the solid-state high-frequency (HF) welder with temperature control. This innovative tool not only offers consistency in welding processes but also allows for enhanced control over the thermal aspects of welding, which is crucial in various applications.
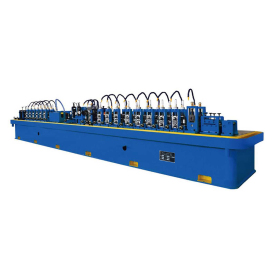
Exploring the Advantages and Applications of Solid State HF Welder with Temperature Control in Modern Manufacturing Processes
High-frequency welding, also known as RF welding, is a technique that utilizes electromagnetic induction to generate heat within the materials being welded. Traditionally, this process relied on vacuum tube technology, which often led to inefficiencies and limited control. However, the advancement of solid-state technology has revolutionized this field. Solid-state HF welders use transistors and other electronic components to generate high-frequency signals, providing a more reliable and energy-efficient solution for welding thermoplastics and a variety of other materials.
The introduction of solid-state technology has led to several intrinsic advantages, including improved reliability and minimized maintenance needs. These welders can operate over a wide range of frequencies, enabling manufacturers to tailor their processes to specific material requirements. One of the most notable advancements in this area is the integration of temperature control mechanisms, which significantly enhances the welding process.
The Role of Temperature Control in Welding
Temperature control in welding is critical to achieving optimal results. The quality of a weld is heavily influenced by the temperature at which materials are joined. Too much heat can lead to melting of the materials beyond the desired area, creating weak spots or imperfections in the weld. Conversely, insufficient heat can result in inadequate fusion, compromising the overall strength and durability of the join.
Solid-state HF welders with integrated temperature control systems can accurately monitor and adjust the welding temperature in real-time. This ability to maintain precise thermal conditions results in consistent weld quality and improves the overall efficiency of the manufacturing process. It also reduces the likelihood of defects, which can lead to costly rework and material waste.
Applications Across Industries
The versatility of solid-state HF welders with temperature control makes them suitable for a multitude of applications across various industries. In the automotive sector, for instance, these advanced welders are often employed to join plastic components in vehicle assembly. The precise control over temperature ensures that the integrity of the parts is maintained, even under the harsh conditions of automotive manufacturing.
In the packaging industry, solid-state HF welders are used for creating strong seals on plastic films and pouches. The ability to control temperature precisely allows for the sealing of materials without compromising the contents of the package, which is critical for food safety and quality. Additionally, industries dealing with medical supplies benefit from this technology, where sterility and reliability are paramount.
Another growing application is in the field of electronics. Solid-state HF welders play a crucial role in the assembly of electronic devices, ensuring that various components are securely joined while minimizing the risk of thermal damage to sensitive electronic parts.
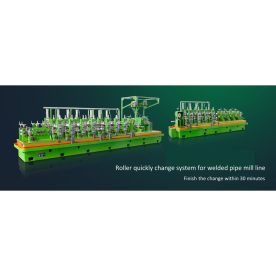
Exploring the Advantages and Applications of Solid State HF Welder with Temperature Control in Modern Manufacturing Processes
One of the most compelling benefits of solid-state HF welders with temperature control is their energy efficiency. Traditional welding technologies often result in significant energy loss through heat dissipation. However, solid-state systems optimize energy usage, leading to reduced operational costs and a lower carbon footprint.

Exploring the Advantages and Applications of Solid State HF Welder with Temperature Control in Modern Manufacturing Processes
Conclusion
Solid-state HF welders with temperature control represent a significant advancement in welding technology, providing manufacturers with the precision and reliability they need to meet modern production demands. Their application across various industries demonstrates their versatility and essential role in achieving high-quality joins in an efficient manner. As industries continue to evolve, the importance of such advanced welding solutions will only grow, paving the way for improved manufacturing processes and sustainable practices. The future of welding is undoubtedly brighter with the incorporation of this innovative technology.