[High frequency welder]Understanding High Frequency Welders: Their Applications, Benefits, and Importance in Modern Manufacturing Processes
News 2024-9-27
High-frequency welding, often simply referred to as high-frequency welding, is a specialized technique that utilizes high-frequency electromagnetic energy to create strong and durable welds. This innovative method is extensively employed in various industries, including textiles, automotive, and plastics. Though invisible to the naked eye, the process is fundamental to modern manufacturing techniques, enhancing productivity and product quality. In this article, we will delve into the intricacies of high-frequency welding, including its applications, benefits, and the reasons why it’s gaining popularity in the industrial sector.
What is High Frequency Welding?
High-frequency welding is a process that uses high-frequency electric currents to join materials, typically plastic or thermoplastics, together. Unlike traditional welding methods that often require heat or pressure, high-frequency welding employs electromagnetic fields, generating heat within the materials themselves through dielectric heating. This results in melting the surfaces of the materials being welded, thereby allowing them to be fused together without the tedious process of external heating.
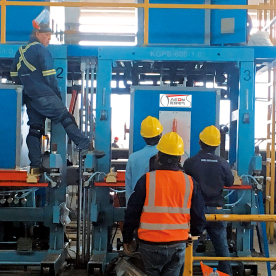
Understanding High Frequency Welders: Their Applications, Benefits, and Importance in Modern Manufacturing Processes
High-frequency welders have a wide range of applications across various industries:
1. **Textile Industry**: One of the primary applications of high-frequency welding is in the textile sector, where it is employed for welding vinyl and PVC fabrics. This is commonly seen in the production of inflatable products like water slides, boats, and soft signage. High-frequency welders enable the creation of seamless, waterproof seams that are essential for these applications.
2. **Automotive Manufacturing**: High-frequency welding is also utilized in the automotive industry, particularly for manufacturing components such as airbag covers and other plastic parts. The technique allows for precise joins that enhance the safety and aesthetics of automotive interiors.
3. **Packaging**: In the packaging industry, high-frequency welders are frequently used for creating secure seals in flexible packaging materials. This is crucial for food packaging, where maintaining freshness and preventing contamination is essential.
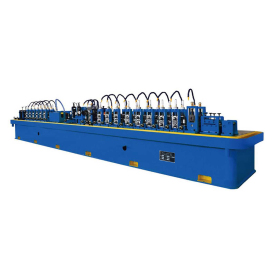
Understanding High Frequency Welders: Their Applications, Benefits, and Importance in Modern Manufacturing Processes
5. **Medical Devices**: The medical field also benefits from high-frequency welding, especially in the production of components like sterile packaging or certain medical devices that require tight seals to maintain sterility.
Benefits of High Frequency Welders

Understanding High Frequency Welders: Their Applications, Benefits, and Importance in Modern Manufacturing Processes
1. **Speed and Efficiency**: High-frequency welding is a rapid process, often allowing for faster production times compared to traditional welding methods. This speed is advantageous in high-volume manufacturing environments, where time is money.
2. **Precision and Consistency**: The use of electromagnetic fields ensures that the welding process is controlled and consistent. This precision reduces the likelihood of defects, resulting in high-quality products that meet industry standards.
3. **Material Versatility**: High-frequency welders can work with a wide range of materials beyond just plastics, including various synthetic fabrics. This versatility makes them a valuable tool in diversified manufacturing operations.
4. **Less Energy Consumption**: As the heat is generated internally within the material, high-frequency welding often requires less overall energy than traditional methods, making it a more environmentally friendly option.
5. **Reduced Equipment Wear**: Since there is no physical contact between the welding electrodes and the materials being welded, wear and tear on equipment are significantly reduced. This longevity can lead to lower maintenance costs and increased uptime.
Conclusion
High-frequency welding is revolutionizing the manufacturing landscape with its speed, precision, and versatility. As industries continue to evolve and demand for higher-quality products escalates, high-frequency welders represent a vital technological advancement. Understanding the applications and benefits of high-frequency welding can equip manufacturers to harness its potential, leading to enhanced productivity and better end products. Whether in the textile industry or the automotive sector, the relevance of high-frequency welders cannot be overstated—they are indeed an essential component of modern manufacturing processes. As these technologies advance, we can anticipate even broader applications and innovations on the horizon.