[Advanced Tube making machinery]Exploring the Innovations and Benefits of Advanced Tube Making Machinery in the Modern Manufacturing Landscape
News 2024-9-26
In today's rapidly evolving manufacturing sector, the emphasis on efficiency, precision, and sustainability is pushing the boundaries of technological advancement. One area that has seen significant developments is the production of pipes and tubes, essential components in various industries such as construction, automotive, aerospace, and energy. Advanced tube making machinery is at the forefront of this transformation, revolutionizing the way these critical products are produced. In this article, we will explore the innovations behind advanced tube making machinery, its benefits, and its impact on the manufacturing landscape.
The Evolution of Tube Making Machinery
Historically, tube making was a labor-intensive process characterized by manual labor and basic mechanical tools. As industries expanded and demand for high-quality products increased, manufacturers recognized the need for more sophisticated machinery that could enhance productivity and product quality. This led to the development of advanced tube making machines that incorporate state-of-the-art technology, programmable automation, and precision engineering.
Modern advanced tube making machinery features high-speed capabilities, allowing manufacturers to produce a larger volume of tubes in a shorter period while maintaining high levels of accuracy. These machines are designed to work with various materials, including stainless steel, aluminum, copper, and plastic, enabling manufacturers to cater to diverse market needs.
Key Innovations in Advanced Tube Making Machinery
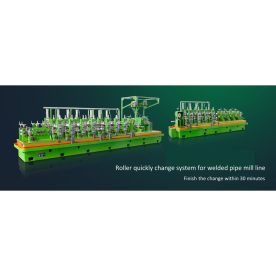
Exploring the Innovations and Benefits of Advanced Tube Making Machinery in the Modern Manufacturing Landscape
2. **Computer Numerical Control (CNC)**: CNC technology has transformed tube making by allowing for highly precise control over machining processes. This technology enables manufacturers to create intricate designs and complex shapes that meet specific industry requirements, eliminating the limitations that traditional methods imposed.
3. **Laser Cutting and Welding**: Advanced tube making machinery often incorporates laser technology, allowing for more accurate cutting and welding processes. Laser cutting reduces material wastage and can create more complex geometries compared to conventional cutting methods, while laser welding provides strong bond integrity without compromising the material's properties.

Exploring the Innovations and Benefits of Advanced Tube Making Machinery in the Modern Manufacturing Landscape
5. **Energy Efficiency**: With growing concerns about environmental sustainability, advanced tube making machinery has been designed to be more energy-efficient. These machines often feature intelligent energy management systems that reduce power consumption, thus lowering operational costs and minimizing the environmental footprint of manufacturing processes.
The Benefits of Advanced Tube Making Machinery
1. **Enhanced Productivity**: The speed and efficiency of advanced tube making machinery significantly boost productivity. Manufacturers can meet increased demand without compromising on quality or increasing labor costs.
2. **Cost-Effectiveness**: While the initial investment in advanced machinery may be high, the long-term savings gained through reduced labor costs, minimized waste, and enhanced production efficiency lead to significant cost-effectiveness.

Exploring the Innovations and Benefits of Advanced Tube Making Machinery in the Modern Manufacturing Landscape
4. **Flexibility**: Modern tube making machines are capable of producing various tube sizes and shapes, offering manufacturers the necessary flexibility to adapt to changing market demands quickly.
5. **Sustainability**: With a focus on energy efficiency and reduced waste generation, advanced tube making machinery aligns with global sustainability initiatives, enabling manufacturers to produce environmentally friendly products.
Conclusion
As manufacturers continue to navigate the complexities of the modern industrial landscape, the role of advanced tube making machinery is becoming increasingly critical. By harnessing innovations in automation, CNC technology, laser processing, and data analytics, manufacturers can enhance productivity, improve product quality, and contribute to a more sustainable future. As the demand for high-quality tubes continues to rise across various industries, investments in advanced machinery will be key to maintaining competitive advantage and meeting customer needs in a dynamic market.