[Roller for tube mill]Understanding the Importance and Functionality of Roller for Tube Mill in Modern Manufacturing Processes
News 2024-9-26
In the world of manufacturing, tube mills play a crucial role in producing various types of tubular products, from simple pipes to complex shapes used in various industries. At the heart of this machinery is a critical component known as the roller, which significantly influences the efficiency and quality of production processes. This article delves deep into the importance and functionality of rollers in tube mills, exploring how they contribute to the overall manufacturing landscape.
The Role of Tube Mills in Manufacturing
A tube mill is a type of machinery specifically designed to produce metal tubes by rolling flat sheets of metal into a cylindrical shape. These mills are widely used in industries such as construction, automotive, aerospace, and oil and gas, where tubular structures are essential components. The process typically involves forming the metal sheet into a tube shape and then welding the edges together to create a seamless finish.
Understanding Rollers
Rollers are vital components in tube mills, ensuring that the metal sheets are accurately shaped and welded to form a high-quality product. They are typically arranged in a series of stands, each playing a specific role throughout the manufacturing process. These rollers come in various sizes and configurations, depending on the tube mill's design and the type of tube being produced.
Key Functions of Rollers in Tube Mills
1. **Shaping**: The primary function of rollers is to shape the metal sheets into the desired tubular form. Using a series of rollers arranged at specific angles, the flat metal is progressively shaped into a cylinder. The design of the rollers must be precise to ensure that the final product meets the required specifications and tolerances.
2. **Alignment**: Rollers help maintain the alignment of the tube as it is being formed. Misalignment can lead to defects in the welded seam, which could compromise the structural integrity of the final product. Advanced tube mills incorporate roller designs that ensure constant alignment throughout the manufacturing process.
3. **Welding**: In many tube mills, the final shaping of the tube includes a welding process to bond the seams. Rollers help hold the edges together during this critical stage, ensuring a uniform and secure weld. The correct pressure and positioning applied by the rollers are essential in achieving a high-quality weld.
4. **Speed and Efficiency**: Rollers are designed to facilitate high-speed production while maintaining product quality. By reducing the number of steps required to shape and weld the tube, the entire production process becomes more efficient, which is vital in a competitive manufacturing environment.
5. **Material Handling**: Rollers also assist in managing the flow of material through the tube mill. They work in conjunction with other machine components to guide the metal sheets into the correct position, reducing the risk of damage or defects during the manufacturing process.
Maintenance and Quality Assurance
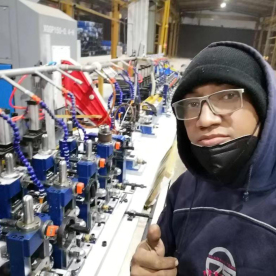
Understanding the Importance and Functionality of Roller for Tube Mill in Modern Manufacturing Processes
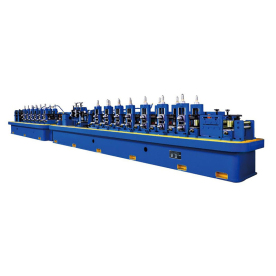
Understanding the Importance and Functionality of Roller for Tube Mill in Modern Manufacturing Processes
Innovations in Roller Design
Advancements in technology have led to the development of sophisticated roller designs equipped with special features to enhance performance. For instance, some rollers are designed with adjustable profiles that can be changed based on the specific requirements of the production process. Additionally, the integration of sensors and automation into roller systems can help monitor alignments and adjust settings in real-time, promoting a further increase in efficiency and reducing the risk of product defects.
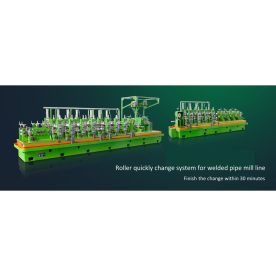
Understanding the Importance and Functionality of Roller for Tube Mill in Modern Manufacturing Processes
In conclusion, rollers for tube mills are integral to the manufacturing of tubular products. Their roles in shaping, aligning, welding, and enhancing the efficiency of the tube mill processes cannot be overstated. As technology continues to evolve, the design and capabilities of these rollers will likely improve, leading to even greater efficiencies and product quality in the manufacturing sector. Understanding the critical nature of rollers in tube mills is essential for manufacturers aiming to optimize their production processes and compete effectively in the ever-evolving market landscape.