[Stainless steel Tube making machine]Understanding the Process and Benefits of a Stainless Steel Tube Making Machine in Modern Manufacturing
News 2024-9-25
****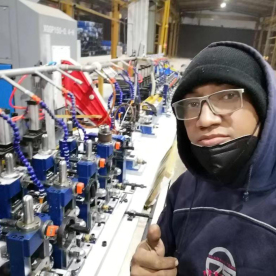
Understanding the Process and Benefits of a Stainless Steel Tube Making Machine in Modern Manufacturing
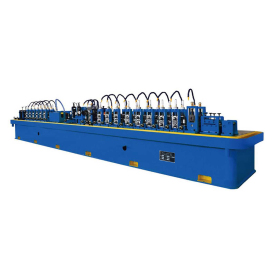
Understanding the Process and Benefits of a Stainless Steel Tube Making Machine in Modern Manufacturing
A stainless steel tube making machine is a specialized piece of equipment designed for the production of stainless steel tubes that meet various application standards. These machines are capable of handling different tube specifications, varying diameters, and wall thicknesses, making them incredibly versatile.
The primary function of these machines is to transform raw stainless steel coils or strips into finished tubes through several processes, including cutting, welding, forming, and finishing. The process typically begins with uncoiling the stainless steel strip, which is then fed into a series of rollers for shaping and forming. The finished tubes can be either seamless or welded, depending on the production requirements.
**Key Features of Stainless Steel Tube Making Machines**
1. **Integrated Control Systems**: Modern stainless steel tube making machines come equipped with advanced digital control systems. This feature allows manufacturers to monitor and adjust the parameters of the production process in real-time, ensuring high precision and reducing the risk of operational errors.
2. **Multi-functional Capabilities**: These machines are designed to accommodate various stainless steel grades and types, providing flexibility in production. Advanced models can produce tubes with different geometries and sizes, making them suitable for numerous applications.

Understanding the Process and Benefits of a Stainless Steel Tube Making Machine in Modern Manufacturing
4. **High Throughput**: Stainless steel tube making machines are engineered for high-speed production, enabling manufacturers to meet increasing demand without compromising on quality. High throughput is achieved through optimized design and automation features.
**Operational Processes Involved in Stainless Steel Tube Production**
The production of stainless steel tubes involves several critical steps, each contributing to the quality and characteristics of the finished product. Here’s a brief overview of the operational processes:
1. **Uncoiling**: The process begins with the unrolling of stainless steel coils. The strips are carefully fed into the machine to avoid deformation.
2. **Forming**: Next, the steel strip undergoes forming, where it is shaped into a cylindrical or desired cross-sectional shape through a series of rollers and guides.
3. **Welding**: Following the forming process, the edges of the tube are welded together. This can be accomplished using various methods, such as TIG (Tungsten Inert Gas) or laser welding, to ensure a strong seam and avoid weak points.
4. **Sizing**: Once welded, the tubes are resized to achieve the desired diameter and wall thickness. This is critical for applications that require precise dimensions.
5. **Finishing**: Finally, the tubes undergo finishing processes, which may include polishing, cleaning, and surface treatment to enhance their aesthetic appeal and resistance to corrosion.
**Benefits of Using Stainless Steel Tube Making Machines**
The advantages of incorporating stainless steel tube making machines into manufacturing processes are manifold:
- **Quality Assurance**: Precision engineering ensures that the tubes produced meet stringent quality standards, which is especially crucial in industries like aerospace and healthcare. - **Cost-Effectiveness**: While the initial investment may be significant, the operational efficiency and reduced waste over time make these machines cost-effective in the long run.
- **Customization**: Manufacturers can cater to specific customer requirements in terms of size, shape, and finish, providing a competitive edge in the market.
- **Scalability**: These machines enable manufacturers to scale production up or down based on demand, allowing for greater flexibility in manufacturing processes.
**Conclusion**
In summary, stainless steel tube making machines play an indispensable role in the contemporary manufacturing sector. They offer efficiency, precision, and reliability, helping industries keep pace with the growing demands for high-quality materials. As technology continues to evolve, the capabilities of these machines will only expand, paving the way for even more innovative applications of stainless steel tubes across various sectors. This not only demonstrates the adaptability of manufacturing technologies but also emphasizes the ongoing importance of stainless steel in industrial applications.