[High frequency welder for plastic]Exploring the Benefits and Applications of High Frequency Welders for Plastic in Modern Manufacturing Processes
News 2024-9-25
****In the ever-evolving world of manufacturing, the need for advanced technologies that enhance productivity and quality is paramount. One such innovation is the high frequency welder for plastic, a tool that has revolutionized the way plastic materials are joined together. With its ability to create strong and reliable bonds, high frequency welding has become an essential technique in various industries, ranging from automotive to medical device manufacturing. This article explores the benefits and applications of high frequency welders for plastic, highlighting why they are indispensable in modern production environments.
Understanding High Frequency Welding
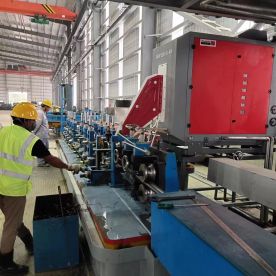
Exploring the Benefits and Applications of High Frequency Welders for Plastic in Modern Manufacturing Processes
Benefits of Using High Frequency Welders for Plastic
1. **Strong and Durable Bonds**: One of the primary advantages of high frequency welding is the formation of strong, permanent bonds. The weld created is often stronger than the original material, providing durability that is essential for many applications, particularly those that require resistance to stress and strain.
2. **Speed and Efficiency**: High frequency welding is a rapid process, which significantly increases productivity in manufacturing environments. The speed of the operation allows companies to produce large volumes of products in a shorter timeframe, which can lead to reduced production costs and enhanced profitability.
3. **Clean and Environmentally Friendly**: Unlike traditional adhesives that may require curing time and can leave residue, high frequency welding produces clean seams with no excess material. This not only results in a neat finish but also minimizes environmental impact, making it a more sustainable option in manufacturing.
4. **Versatility**: High frequency welders can be used to join a wide variety of plastic materials, including PVC, polyurethane, and polyester, among others. This versatility makes them suitable for a broad range of applications, further solidifying their place in an array of industries.
5. **Precision and Control**: The high frequency welding process allows for precise control over the welding parameters, including time, pressure, and temperature. This level of control ensures consistent quality in the welds and minimizes the risk of defects, which is particularly important in industries where product integrity is critical.
Applications Across Industries
High frequency welders for plastic have found applications in several sectors:
- **Automotive Industry**: In the automotive sector, high frequency welding is used to manufacture components such as dashboards, air ducts, and fuel tanks. The strong and lightweight welds contribute to the overall performance and safety of vehicles.
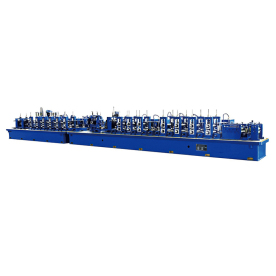
Exploring the Benefits and Applications of High Frequency Welders for Plastic in Modern Manufacturing Processes
- **Textile Industry**: High frequency welding is also prevalent in the textile industry, particularly for creating seams in technical textiles and inflatable products like life rafts and tents. The waterproof and airtight characteristics of high frequency welded seams make them ideal for applications where exposure to liquids or gases is a concern.
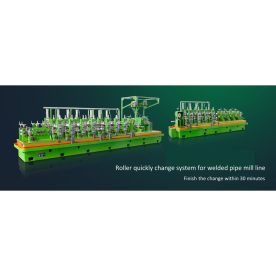
Exploring the Benefits and Applications of High Frequency Welders for Plastic in Modern Manufacturing Processes
Conclusion
As industries continue to demand innovative solutions for joining plastic materials, high frequency welders for plastic stand out as a powerful tool that addresses these needs comprehensively. Offering numerous benefits such as strong bonds, speed, efficiency, and versatility, these welders have firmly established themselves in the manufacturing landscape. As technology advances and the manufacturing process becomes increasingly sophisticated, high frequency welding is poised to play an even greater role in enhancing product quality and operational efficiency across various sectors.