[High-efficiency pipe mill production line]Revolutionizing Metal Fabrication: An In-Depth Look at High-Efficiency Pipe Mill Production Lines and Their Impact on Industry Standards
News 2024-9-25
****In today’s fast-paced manufacturing environment, efficiency and productivity are paramount. Industries across the globe are continuously seeking ways to enhance their operations, reduce waste, and improve the quality of their products. One area where significant advancements have been made is in the field of pipe manufacturing. High-efficiency pipe mill production lines have emerged as game-changers, enabling manufacturers to produce high-quality pipes at unprecedented speeds and reduced costs. In this article, we will explore the components, advantages, and future of high-efficiency pipe mill production lines in detail.
Understanding High-Efficiency Pipe Mill Production Lines
A high-efficiency pipe mill production line comprises various advanced machinery and technology designed to optimize the production of pipes. These production lines are responsible for the seamless operation of multiple processes, including pipe forming, welding, and finishing. High-efficiency lines utilize automated systems and computerized controls that ensure consistent quality while minimizing human error.
The construction of these production lines typically includes several key components, such as:
1. **Steel Strip Rollers**: This part of the production line feeds raw steel strips into the pipe mill. These rollers manipulate the strips into the desired pipe shape. 2. **Welding Units**: After the pipe is formed, it enters the welding stage, where high-frequency or laser welding techniques are used to create strong, durable seams.
3. **Cooling and Sizing Sections**: Post-welding, pipes go through cooling and sizing units to ensure they are dimensionally accurate and free from defects.
4. **Quality Inspection Systems**: Integrated inspection systems using laser technology and cameras ensure that each pipe meets strict industry specifications.
5. **Finishing Equipment**: Finally, the pipes undergo further finishing processes such as beveling, coating, or surface treatment, enhancing their durability and appearance before shipping.
Advantages of High-Efficiency Pipe Mill Production Lines
The implementation of high-efficiency pipe mill production lines confers a multitude of advantages to manufacturers:
1. **Increased Productivity**: One of the most significant benefits of high-efficiency pipe mills is increased output. These production lines can operate at high speeds without compromising quality, allowing manufacturers to meet soaring market demands.
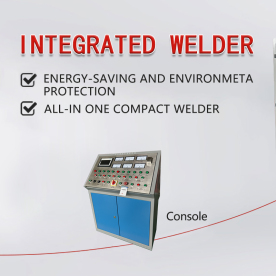
Revolutionizing Metal Fabrication: An In-Depth Look at High-Efficiency Pipe Mill Production Lines and Their Impact on Industry Standards
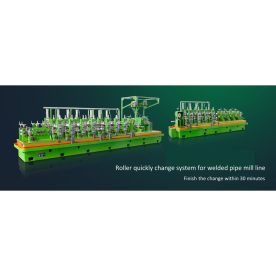
Revolutionizing Metal Fabrication: An In-Depth Look at High-Efficiency Pipe Mill Production Lines and Their Impact on Industry Standards
4. **Cost-Effectiveness**: While the initial investment in high-efficiency pipe mill production lines can be substantial, the long-term savings in labor, material costs, and reduced error rates often outweigh the upfront costs.
5. **Flexibility**: Many high-efficiency production lines are designed with adaptability in mind, enabling manufacturers to produce various types and sizes of pipes without extensive reconfiguration.
Future Trends in High-Efficiency Pipe Mill Production Lines
The future of high-efficiency pipe mill production lines is bright, driven by ongoing technological advancements. Emerging trends include:
- **Industry 4.0 Integration**: The use of the Internet of Things (IoT), artificial intelligence (AI), and machine learning is becoming more prevalent in pipe manufacturing. These technologies facilitate real-time monitoring, predictive maintenance, and enhanced decision-making.
- **Sustainability Initiatives**: As industries face increasing pressure to adopt environmentally friendly practices, pipe manufacturers are innovating sustainable production techniques, including using recycled materials and reducing energy consumption.
- **Smart Manufacturing**: The growth of smart manufacturing processes allows for improved feedback loops in production lines, enabling quicker adjustments to enhance efficiency and quality proactively.

Revolutionizing Metal Fabrication: An In-Depth Look at High-Efficiency Pipe Mill Production Lines and Their Impact on Industry Standards
High-efficiency pipe mill production lines represent a significant leap forward in pipe manufacturing technology. The benefits of increased productivity, reduced waste, improved quality, and cost-effectiveness make them an essential investment for manufacturers aiming to thrive in a competitive market. As technology continues to evolve and shape the landscape of manufacturing, the pipes produced on these high-efficiency lines will be crucial in supporting global infrastructure and industrial needs. Embracing these advancements will undoubtedly redefine industry standards and foster a new era of manufacturing excellence.