[High-efficiency All-in-one Welding System]Exploring the Advantages of a High-Efficiency All-in-One Welding System for Modern Manufacturing and Repair Applications
News 2024-9-23
****In the ever-evolving landscape of manufacturing and industrial repair, the quest for efficiency and productivity is paramount. Among the various tools and technologies making waves in this sector, the high-efficiency all-in-one welding system stands out as an innovative solution that meets the demands of modern fabrication. These versatile machines combine multiple welding techniques in one cohesive unit, providing a range of benefits for operators and businesses alike. This article delves into the specific advantages of high-efficiency all-in-one welding systems, covering their design, applications, and impact on productivity.
Understanding the All-in-One Welding System
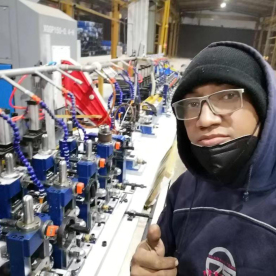
Exploring the Advantages of a High-Efficiency All-in-One Welding System for Modern Manufacturing and Repair Applications
Increased Efficiency and Productivity
One of the most compelling reasons for adopting high-efficiency all-in-one welding systems is the significant boost in efficiency and productivity they offer. Traditionally, welders would need to set up various machines to accommodate different welding processes, leading to increased downtime, wasted materials, and higher labor costs. With an all-in-one system, operators can efficiently switch between processes, minimizing the time spent on setup and adjustments.
Additionally, these systems are often equipped with features that optimize the welding process. For instance, advanced arc control technologies can lead to cleaner, stronger welds while reducing spatter and improving consistency. As a result, businesses can not only complete projects faster but also improve the overall quality of their work, leading to enhanced customer satisfaction and repeat business.
Cost-Effectiveness
Investing in a high-efficiency all-in-one welding system can also provide significant long-term cost savings. By reducing downtime and the need for multiple machines, these systems lower operational costs. Furthermore, their ability to produce high-quality welds consistently helps minimize material waste, which can be a critical factor in manufacturing budgets.
Moreover, the reduced need for repairs and maintenance associated with simpler, more efficient machines can contribute to lower operational expenses. This cost-effectiveness makes high-efficiency all-in-one welding systems attractive not only for large manufacturers but also for small and medium-sized enterprises looking to maximize their budget.
Versatility Across Applications
The versatility of all-in-one welding systems makes them suitable for various applications, from automotive repair to construction and metal fabrication. No matter the industry, the ability to perform multiple welding processes in one location simplifies workflows. For instance, automotive technicians can easily switch from MIG welding for frame repairs to TIG welding for precision work on intricate components without the need for additional setup or equipment. This adaptability allows businesses to tackle a diverse range of projects, expanding their service offerings and enhancing profitability.
Enhanced Training and Safety
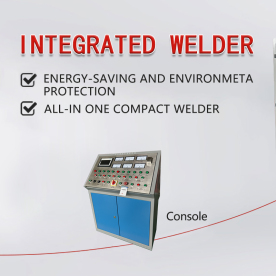
Exploring the Advantages of a High-Efficiency All-in-One Welding System for Modern Manufacturing and Repair Applications

Exploring the Advantages of a High-Efficiency All-in-One Welding System for Modern Manufacturing and Repair Applications
High-efficiency all-in-one welding systems represent a significant advancement in welding technology, providing unparalleled productivity, cost-effectiveness, and versatility. As industries continue to embrace the need for efficiency and quality, these systems are likely to become even more integral to the welding landscape. By investing in an all-in-one solution, businesses can enhance their operational capabilities, improve their bottom line, and stay competitive in a rapidly changing market. As the future unfolds, the all-in-one welding system will undoubtedly play a pivotal role in driving the next generation of manufacturing excellence.