[Pipe making machine with welding function]Revolutionizing Pipe Production: The Impact of Advanced Pipe Making Machines with Welding Function on Manufacturing Efficiency
News 2024-9-21
In the competitive landscape of manufacturing, the innovation and technological advancement in equipment have become pivotal to enhancing productivity and efficiency. Among the most significant advancements in the realm of industrial machinery is the emergence of pipe making machines with welding functions. These machines offer manufacturers a streamlined solution to produce high-quality pipes swiftly and efficiently while minimizing labor costs and maximizing output. This article delves into the features, advantages, and applications of pipe making machines equipped with welding functions, highlighting their transformative role in various industries.
Understanding Pipe Making Machines with Welding Function
A pipe making machine with welding function is a specialized industrial unit designed to produce pipes from various raw materials, including metal, plastic, and composite materials. The intrinsic feature that sets these machines apart is their welding capability, allowing for the continuous production of seamless pipes. The welding function is typically integrated into the machine’s design, enabling the joining of pipe segments or the formation of long lengths of pipe without the need for additional processes.
The production process generally involves feeding raw material into the machine, where it is shaped and welded at high speed. Depending on the type of machine, manufacturers can create different pipe sizes, shapes, and thicknesses, catering to diverse market needs.
Key Features and Technologies
Modern pipe making machines with welding functions are equipped with advanced technologies that enhance their operational efficiency. Some of the notable features include:
1. **Automated Control Systems**: Most advanced pipe making machines utilize programmable logic controllers (PLC) and user-friendly interfaces. This enables operators to easily adjust parameters, monitor production metrics, and troubleshoot issues in real-time.
2. **High-Speed Welding Technologies**: The incorporation of high-frequency induction welding or laser welding technology allows for rapid and reliable welding of pipe joints, resulting in stronger seams and reduced production time.
3. **Versatile Material Handling**: These machines often support various materials like stainless steel, carbon steel, and multi-layer composites, providing flexibility to manufacturers in meeting specific market demands.
4. **Efficient Cooling Systems**: Adequate cooling mechanisms ensure that welded pipes maintain dimensional accuracy and structural integrity, which is crucial for high-performance applications.
5. **Easy Maintenance Features**: Modern designs focus on ease of maintenance, allowing for quick parts replacement and efficient cleaning processes, reducing downtime and enhancing productivity.
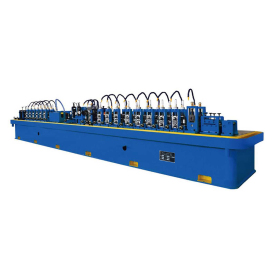
Revolutionizing Pipe Production: The Impact of Advanced Pipe Making Machines with Welding Function on Manufacturing Efficiency
The integration of welding functions in pipe making machines brings several advantages to manufacturers, including:
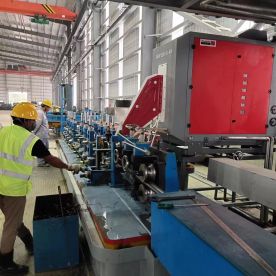
Revolutionizing Pipe Production: The Impact of Advanced Pipe Making Machines with Welding Function on Manufacturing Efficiency
- **Cost-Effectiveness**: By minimizing the need for manual labor and reducing waste material thanks to precision welding techniques, these machines offer a more cost-effective solution for pipe production.
- **Improved Product Quality**: Seamless welding leads to stronger and more durable pipes, allowing for enhanced performance in demanding applications, such as oil and gas transportation, construction, and fluid systems.
- **Flexibility in Design**: Manufacturers can easily adjust parameters for different pipe specifications, allowing for custom production runs that align with client requirements.
Applications Across Industries
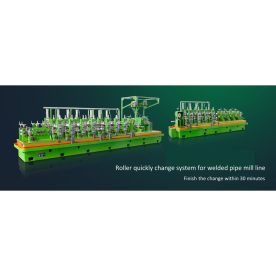
Revolutionizing Pipe Production: The Impact of Advanced Pipe Making Machines with Welding Function on Manufacturing Efficiency
Conclusion
As industries continue to evolve and demand for high-quality, efficient production methods grows, the significance of pipe making machines with welding functions becomes increasingly clear. These innovative machines not only enhance production capabilities but also drive cost savings and improve product quality. By adopting advanced pipe making technologies, manufacturers position themselves for success in an ever-competitive market, ensuring they meet the varying demands of their customers while upholding the standards of modern manufacturing.