[High frequency welder]Exploring the High Frequency Welder: Revolutionizing Metal Joining Techniques for Enhanced Durability and Efficiency in Modern Manufacturing
News 2024-9-21
In the ever-evolving landscape of manufacturing, the quest for stronger, more reliable, and efficient metal joining techniques has led to the widespread adoption of high-frequency welding. This innovative process has transformed how industries join metal components, offering a host of advantages over traditional welding methods. In this article, we will delve into the workings of a high-frequency welder, its applications, benefits, and its future in the manufacturing world.
Understanding High Frequency Welding
High-frequency welding, also known as high-frequency induction welding or RF welding, is a specialized welding technique that utilizes high-frequency electromagnetic waves to heat the surface of metal materials. The process typically involves the use of a high-frequency welder, which generates electromagnetic energy in the radio frequency range (usually between 3 MHz and 30 MHz). This energy creates an electric field that causes the conductive metal to heat up rapidly, allowing for precise joining of materials without extensive thermal input.
The process usually entails placing the metal pieces to be joined within a specially designed welding tool, along with an electrode. When the high-frequency welder is activated, the electromagnetic waves create rapid oscillations that generate heat at the surface of the metal. The resulting heat softens the metal, enabling it to flow together and form a strong bond as it cools. The speed of the process and the localized heating involved minimize the risk of distortion, ensuring high-quality welds.
Applications of High Frequency Welders
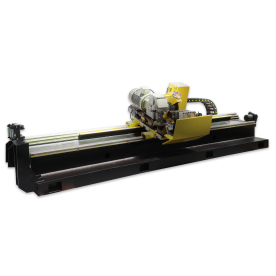
Exploring the High Frequency Welder: Revolutionizing Metal Joining Techniques for Enhanced Durability and Efficiency in Modern Manufacturing
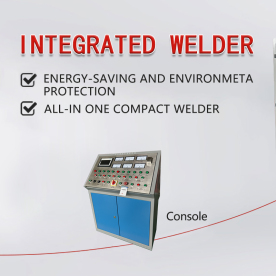
Exploring the High Frequency Welder: Revolutionizing Metal Joining Techniques for Enhanced Durability and Efficiency in Modern Manufacturing
2. **Aerospace Sector**: Given the stringent requirements for strength and reliability in aerospace applications, high-frequency welding is employed for joining critical components in aircraft and spacecraft. The lightweight stitch welds created through this process help reduce overall weight while ensuring structural integrity.
3. **Pipeline Fabrication**: High-frequency welders are ideal for the production of pipelines, especially in the oil and gas industry. The speed and efficiency of the process are essential for meeting industry demands, where durability and corrosion resistance are paramount.
4. **Consumer Goods**: In manufacturing consumer goods, such as kitchen appliances and various metal products, high-frequency welding offers precision and high-quality finishes. It is used to join components while maintaining aesthetic appeal and functionality.
Benefits of High Frequency Welders
The adoption of high-frequency welders brings several distinct advantages to the manufacturing process:
1. **Speed and Efficiency**: One of the most significant benefits of high-frequency welding is the speed at which it can create strong welds. The process can often be completed in seconds, allowing for increased production rates and reduced cycle times.
2. **Reduced Thermal Impact**: Unlike traditional welding methods that can cause extensive thermal distortion, high-frequency welders apply concentrated heat only to the areas being welded. This local heating mitigates warping and maintains the integrity of surrounding materials.
3. **Enhanced Weld Quality**: The precision offered by high-frequency welders results in high-quality welds that are strong, consistent, and reliable. The welding process is less prone to defects such as cracks or incomplete joints.
4. **Energy Efficiency**: High-frequency welders typically consume less energy compared to other welding methods. The focused application of heat means less energy waste, making it a more environmentally friendly option.
5. **Versatility**: High-frequency welders can be used to join a wide range of materials, including steel, aluminum, copper, and various alloys. This versatility enables manufacturers to adapt the technology to meet diverse production needs.

Exploring the High Frequency Welder: Revolutionizing Metal Joining Techniques for Enhanced Durability and Efficiency in Modern Manufacturing
As industries continue to seek innovative solutions for metal joining, the role of high-frequency welders is poised to expand. With advancements in technology, including automation and enhanced control systems, the efficiency and effectiveness of high-frequency welding will likely improve, leading to more widespread adoption across various sectors.
In addition, as sustainability becomes an increasing priority for manufacturers, the energy efficiency and waste reduction associated with high-frequency welding will make it an appealing option. As economies around the world evolve, embracing cleaner and more efficient manufacturing processes will be crucial for meeting environmental goals and maintaining competitive advantage.
In conclusion, the high-frequency welder represents a significant advancement in metal joining technology. Its rapid, precise, and reliable welding capabilities make it a valuable asset in modern manufacturing. As industries continue to innovate and adapt, the high-frequency welder will remain at the forefront of effective metal joining techniques, driving progress in countless applications.