[Automatic ERW tube mill equipment]Harnessing Innovation: The Essential Role of Automatic ERW Tube Mill Equipment in Modern Manufacturing Processes
News 2024-9-20
****In today’s fast-paced industrial environment, efficiency and precision are paramount. Among the key players in manufacturing technology is the Automatic Electric Resistance Welded (ERW) Tube Mill Equipment, a critical component for producing high-quality tubes and pipes for various applications. This equipment revolutionizes the creation of steel tubes, enhancing productivity, reducing labor costs, and improving the overall quality of the finished product. In this article, we will explore the significant advantages of Automatic ERW Tube Mill Equipment and its impact on today’s manufacturing industries.
Understanding ERW Tube Mill Equipment
At its core, Electric Resistance Welding (ERW) is a process that uses electric current to weld materials together. The ERW tube milling process involves forming a flat strip of steel into a cylindrical shape and then using electric resistance welding to fuse the edges. Automatic ERW Tube Mill Equipment streamlines and automates this process, allowing manufacturers to produce tubes of various sizes and specifications with high precision.
Key Components of Automatic ERW Tube Mill Equipment
The Automatic ERW Tube Mill Equipment consists of several essential components, each playing a vital role in the manufacturing process:
1. **Uncoiler:** The uncoiler unwinds the steel strip, feeding it into the forming section of the mill. Automation in this area ensures minimal downtime and maximizes material usage.
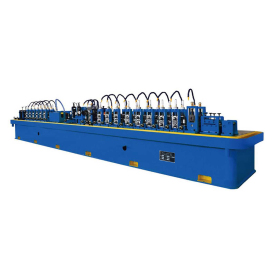
Harnessing Innovation: The Essential Role of Automatic ERW Tube Mill Equipment in Modern Manufacturing Processes
3. **Welding Section:** The edges of the formed tube are then brought together before being welded through the electric resistance method. This equipment ensures consistent weld quality, which is crucial for structural integrity.
4. **Sizing Section:** This section standardizes the diameter and shape of the tubes. Advanced technology allows for precise adjustments, ensuring uniformity across the batch.
5. **Cut-off Section:** Once the desired length is achieved, the tubes are cut accurately and efficiently. Automation ensures rapid production rates while minimizing waste.
6. **Packaging and Stacking:** Automated systems also handle the packing and stacking of the finished tubes, preparing them for shipment without the need for extensive manual labor.
Advantages of Automatic ERW Tube Mill Equipment
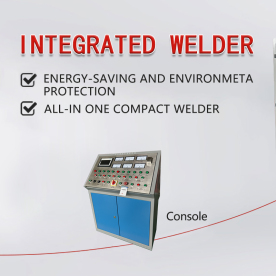
Harnessing Innovation: The Essential Role of Automatic ERW Tube Mill Equipment in Modern Manufacturing Processes
2. **Enhanced Quality Control:** Advanced sensors and monitoring systems built into the equipment allow for real-time quality control, ensuring that each tube meets the required specifications. This level of scrutiny leads to fewer defects and higher customer satisfaction.
3. **Flexible Production Capabilities:** Many modern Automatic ERW Tube Mill systems are designed with flexibility in mind, capable of producing various types and sizes of tubes. This adaptability makes it easier for manufacturers to respond to changing market demands.
4. **Lower Production Costs:** By minimizing labor requirements and reducing waste, automatic mills contribute to significantly lowered production costs. These savings can be passed on to customers, providing a competitive edge in the market.
5. **Improved Safety:** Automation enhances workplace safety by reducing the need for personnel to be in close proximity to potentially hazardous machinery. The risks associated with manual handling and intervention are thus minimized.
The Future of Automatic ERW Tube Mill Equipment

Harnessing Innovation: The Essential Role of Automatic ERW Tube Mill Equipment in Modern Manufacturing Processes
In conclusion, Automatic ERW Tube Mill Equipment plays a crucial role in shaping the future of manufacturing. By embracing this technology, companies can enhance their productivity, improve product quality, and remain competitive in an increasingly challenging marketplace. As industries continue to evolve, investment in such advanced equipment will be integral to achieving operational excellence.