[All-in-one High Frequency Welder for Automotive Industry]Revolutionizing Automotive Manufacturing: The Impact of All-in-One High Frequency Welder for the Automotive Industry
News 2024-9-19
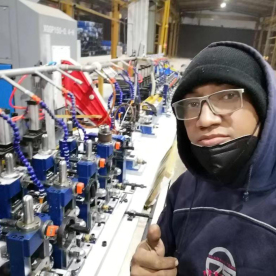
Revolutionizing Automotive Manufacturing: The Impact of All-in-One High Frequency Welder for the Automotive Industry
Traditional welding methods, while effective, often require multiple machines and setups for different applications, leading to increased costs and time. The All-in-One High Frequency Welder addresses these challenges by integrating various welding processes into a single unit. This means that manufacturers can perform numerous welding operations, such as spot welding, seam welding, and even some types of plastic welding, without needing to switch between different machines. This versatility makes it an invaluable tool in the automotive assembly line where efficiency and precision are paramount.
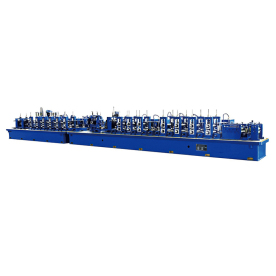
Revolutionizing Automotive Manufacturing: The Impact of All-in-One High Frequency Welder for the Automotive Industry
In addition to its versatility, the All-in-One High Frequency Welder is designed to enhance the quality of welds produced. High frequency welding is known for its precision and control, enabling manufacturers to achieve cleaner and stronger welds. The ability to precisely control the weld parameters, such as the frequency and amplitude, means that welds can be tailored to meet specific requirements for different components and materials. This results in not only improved product quality but also reduced waste, as the likelihood of defects is minimized.
Moreover, the integration of advanced technology such as automation and smart sensors into All-in-One High Frequency Welders has further revolutionized the welding process in the automotive industry. Automated systems can monitor the welding process in real-time, adjusting parameters as needed to ensure optimal performance. This level of automation not only increases production speed but also reduces the chances of human error, thereby contributing to overall quality assurance.
From an economic standpoint, the implementation of All-in-One High Frequency Welders can lead to significant cost savings for automotive manufacturers. The reduction in the number of machines required not only decreases capital investments but also lowers maintenance costs and minimizes the amount of factory floor space needed for welding operations. Additionally, the improved welding quality and efficiency lead to a decrease in production times, resulting in faster turnaround and increased output.
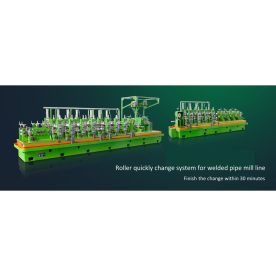
Revolutionizing Automotive Manufacturing: The Impact of All-in-One High Frequency Welder for the Automotive Industry
In conclusion, the All-in-One High Frequency Welder represents a significant leap forward in automotive manufacturing technology. By providing versatility, precision, and efficiency, it addresses many challenges faced by the industry today. As automotive manufacturers strive to keep pace with rapidly changing consumer demands and technological advancements, investing in this cutting-edge welding solution not only enhances production capabilities but also supports the overarching goals of quality, sustainability, and innovation. As we look to the future, the All-in-One High Frequency Welder is set to play a pivotal role in shaping the landscape of the automotive industry.