[Precision ERW tube mill machinery]Exploring the Advantages and Innovations of Precision ERW Tube Mill Machinery in Modern Manufacturing Industries
News 2024-9-16
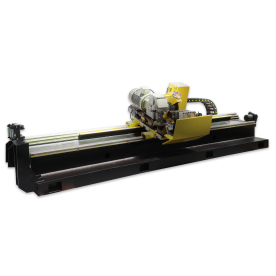
Exploring the Advantages and Innovations of Precision ERW Tube Mill Machinery in Modern Manufacturing Industries
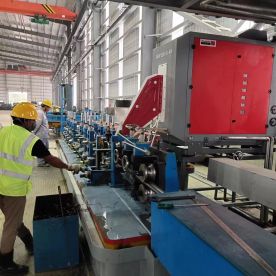
Exploring the Advantages and Innovations of Precision ERW Tube Mill Machinery in Modern Manufacturing Industries
One of the most significant benefits of Precision ERW tube mill machinery is its ability to produce tubes with a high degree of dimensional accuracy. Precision is critical in applications such as automotive, aerospace, and construction, where even minor deviations can lead to functional failures or safety concerns. ERW machinery is engineered to maintain tight tolerances, ensuring that each product meets the rigorous standards required in these industries. Advanced computer numerical control (CNC) systems further enhance the precision of the tube mill, enabling manufacturers to produce complex profiles and sizes according to customer specifications.
In recent years, advancements in Precision ERW tube mill technology have led to the integration of automation and Industry 4.0 concepts. Modern tube mills are equipped with sophisticated sensors and monitoring systems that provide real-time feedback during production. This capability allows for immediate adjustments to be made, reducing downtime and maintaining optimal production rates. Furthermore, automation minimizes human error, leading to higher product quality and consistency.
Additionally, Precision ERW tube mill machinery has become increasingly energy-efficient. As industries worldwide emphasize sustainability and reducing carbon footprints, manufacturers are integrating energy-saving features into their machines. Advances in welding technology and heat management systems significantly lower energy consumption, making the overall production process not only more cost-effective but also environmentally responsible. By focusing on energy efficiency, companies can enhance their competitiveness while contributing positively to global sustainability efforts.
Another noteworthy aspect of Precision ERW tube mill machinery is its versatility. Manufacturers can produce a wide variety of tube sizes, shapes, and thicknesses, allowing them to cater to diverse markets. From small diameter tubes used in furniture manufacturing to large structural pipes used in construction projects, ERW tube mills can adapt to changing customer demands without the need for extensive retooling.
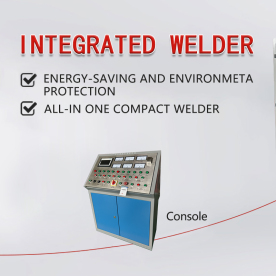
Exploring the Advantages and Innovations of Precision ERW Tube Mill Machinery in Modern Manufacturing Industries
The landscape of manufacturing will continue to evolve, and Precision ERW tube mill machinery is at the forefront of this transformation. As competition intensifies and customer expectations rise, companies that embrace these advanced technologies will likely lead the market. The ability to produce high-quality, precise tubes quickly and efficiently is not just a competitive advantage—it's becoming a necessity.
As industry leaders look toward the future, investing in state-of-the-art Precision ERW tube mill machinery will undoubtedly play a critical role in shaping manufacturing processes. By harnessing the power of innovation, precision engineering, and sustainability, companies can achieve greater productivity while meeting the evolving demands of the global marketplace. With these advancements, the future looks promising for industries reliant on tube and pipe products, reinforcing the pivotal role of ERW technology in modern manufacturing.