[All-in-one high frequency welder]Exploring the Benefits and Applications of All-in-One High Frequency Welders in Modern Manufacturing Industries
News 2024-9-15
In the realm of modern manufacturing, the demand for precision and efficiency is at an all-time high. Businesses constantly seek advanced technologies that not only enhance production capabilities but also deliver high-quality outputs. One of the most remarkable advancements in this field is the introduction of all-in-one high frequency welders. These machines deliver unparalleled performance, efficiency, and versatility, making them invaluable assets across various industries.
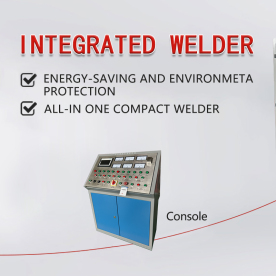
Exploring the Benefits and Applications of All-in-One High Frequency Welders in Modern Manufacturing Industries
**Key Features of All-in-One High Frequency Welders**
All-in-one high frequency welders are distinguished by their multifaceted capabilities. They typically feature advanced digital controls that allow operators to easily adjust settings for different materials, ensuring optimal weld quality and efficiency. These welders can often handle a range of tasks, including welding, cutting, and sealing, making them suitable for varied applications.
Moreover, these machines are engineered to minimize energy consumption. The high frequency technology operates efficiently, significantly reducing running costs while maintaining a consistent output. This energy efficiency is not only beneficial for the bottom line but also supports sustainable manufacturing practices, a growing concern for many industries today.
**Applications Across Industries**
The versatility of all-in-one high frequency welders enables them to be utilized across multiple sectors. In the textile industry, for example, these welders can be used for joining synthetic fabrics, creating waterproof seams, and producing durable outdoor gear. Their ability to produce strong, reliable bonds without compromising the material’s integrity makes them ideal for applications requiring flexibility and durability.
In the automotive sector, these welders are utilized for manufacturing components such as airbags and various interior parts that require precise seams. The high efficiency of these machines ensures quick production times, which is crucial for industries that operate on tight schedules while maintaining the high-quality standards expected in automotive manufacturing.
The packaging industry also benefits from all-in-one high frequency welders. They can effectively create hermetic seals for food and pharmaceutical products, thus enhancing product preservation and safety. The flexibility of these machines to adapt to different packaging materials helps businesses meet diverse client needs and stay competitive in a constantly evolving market.
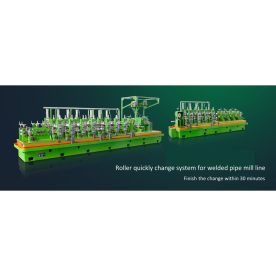
Exploring the Benefits and Applications of All-in-One High Frequency Welders in Modern Manufacturing Industries
The economic benefits of integrating an all-in-one high frequency welder into manufacturing operations are significant. By eliminating the need for multiple pieces of equipment, businesses can save on initial capital expenditures and ongoing maintenance costs. Moreover, with fewer machines to operate, training for staff becomes more straightforward, enhancing overall operational efficiency.
In addition, the rapid production capabilities of these welders help reduce lead times. Faster turnaround allows businesses to meet customer demands more effectively, creating a direct positive impact on customer satisfaction and loyalty. The ability to easily switch between different settings also reduces downtime and enhances productivity.
**Conclusion**

Exploring the Benefits and Applications of All-in-One High Frequency Welders in Modern Manufacturing Industries
In conclusion, the integration of these advanced welders showcases a commitment to embracing the future of manufacturing, where technology and innovation play critical roles in driving business success. Whether you’re a small-scale manufacturer or part of a large industrial operation, the advantages offered by all-in-one high frequency welders can elevate your production capabilities and set you apart in a competitive marketplace.