[Pipe mill production line with quality control measures]Enhancing Efficiency and Reliability: Pipe Mill Production Line with Robust Quality Control Measures for Superior Product Standards
News 2024-9-14
The pipe manufacturing industry has seen significant advancements in technology and machinery over the years, notably in the evolution of pipe mill production lines. These production lines are critical in delivering high-quality pipes used in various sectors such as construction, oil and gas, and water management. As the demand for reliable and durable piping solutions grows, the implementation of effective quality control measures has emerged as a non-negotiable aspect of the production process. This article delves into the components of a modern pipe mill production line and the importance of quality control measures within this framework.
A typical pipe mill production line comprises several interconnected processes, including steel strip preparation, welding, forming, and finishing. The line usually starts with steel coils that are unwound and fed into the mill. The steel strip is then shaped into a tube using rollers, after which the edges are welded together utilizing electric welding techniques. This process not only ensures the structural integrity of the pipes but also allows for the seamless production of varying diameters and wall thicknesses. The versatility of these production lines enables manufacturers to cater to diverse specifications required by clients across different industries.
However, producing pipes efficiently is only half the battle. Ensuring these pipes meet strict quality standards is imperative for maintaining customer trust and satisfaction. Quality control is an ongoing process that involves rigorous inspection and testing at various stages of the production line. Effective quality control measures encompass several techniques and methodologies to ensure each product conforms to industry standards and regulatory requirements.
One essential quality control measure employed in the pipe mill production line is the use of Non-Destructive Testing (NDT). NDT techniques, such as ultrasonic testing, magnetic particle inspection, and dye penetrant testing, allow for the detection of internal and external defects in the pipes without causing any damage. For instance, ultrasonic testing can identify potential flaws in welds that may compromise the structural integrity of the pipes. By incorporating NDT at critical stages of the production process, manufacturers can preemptively address potential issues before the final product is completed.
Moreover, real-time monitoring of the production line plays a crucial role in ensuring quality control. Integrating advanced automation and data analytics solutions allows for the continuous tracking of production metrics. Key performance indicators (KPIs) such as temperature, pressure, and material properties are monitored to ensure they remain within predefined limits. If deviations occur, operators are alerted immediately, enabling them to take corrective action and maintain the consistency of the production output.
Another integral component of quality control within pipe mill production lines is the establishment of standardized procedures for each phase of the manufacturing process. These standard operating procedures (SOPs) delineate specific steps to be followed, along with the necessary checks and balances. Regular training and refresher courses ensure that all personnel are well-versed in these procedures, reinforcing the significance of quality control in their daily operations.
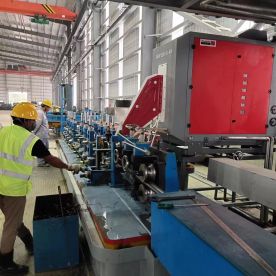
Enhancing Efficiency and Reliability: Pipe Mill Production Line with Robust Quality Control Measures for Superior Product Standards
To further ensure quality assurance, many pipe manufacturing plants have adopted third-party testing and certification processes. Independent organizations assess the pipes to validate their compliance with industry standards, providing additional credibility and reassurance to clients. These external audits are vital in fostering transparency and building long-term relationships with customers who seek reliability in their piping solutions.
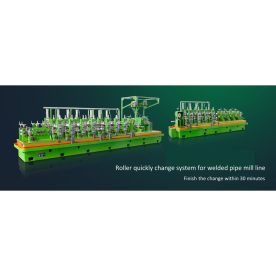
Enhancing Efficiency and Reliability: Pipe Mill Production Line with Robust Quality Control Measures for Superior Product Standards
