[High-efficiency ERW tube mill]Revolutionizing the Industry: The Impact of High-Efficiency ERW Tube Mill Technology on Modern Manufacturing Processes
News 2024-9-14
****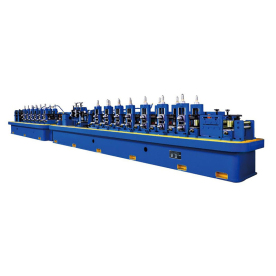
Revolutionizing the Industry: The Impact of High-Efficiency ERW Tube Mill Technology on Modern Manufacturing Processes
At its core, the high-efficiency ERW tube mill is designed for the production of high-quality steel tubes and pipes through the electric resistance welding process. Unlike traditional methods, which may involve longer lead times and greater resource consumption, the high-efficiency version streamlines operations and minimizes waste. This is primarily achieved through a combination of optimized welding technology and advanced automation, which together facilitate faster production rates and improved consistency, thus making it possible to produce tubes that meet stringent industry standards.
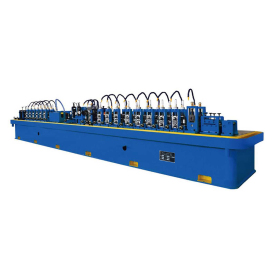
Revolutionizing the Industry: The Impact of High-Efficiency ERW Tube Mill Technology on Modern Manufacturing Processes
Moreover, the emphasis on energy efficiency in the design of high-efficiency ERW tube mills cannot be overstated. These modern machines are equipped with energy-saving technology that reduces power consumption during operation. As energy costs continue to rise, the ability to produce more while using less power translates into substantial savings for manufacturers. This reduced environmental impact is also increasingly appealing to companies looking to enhance their sustainability initiatives, and investing in high-efficiency machinery represents a commitment to both cost savings and eco-friendliness.
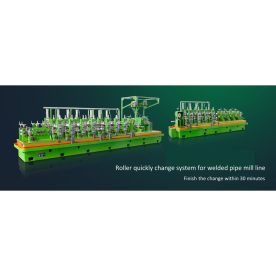
Revolutionizing the Industry: The Impact of High-Efficiency ERW Tube Mill Technology on Modern Manufacturing Processes
Another advantage of the high-efficiency ERW tube mill is its versatility. These mills can accommodate a wide range of materials and sizes, allowing producers to diversify their product offerings without undergoing significant downtime or the need for specialized equipment. Manufacturers can switch between different tube dimensions or material grades with relative ease, enabling them to respond quickly to changing market demands and customer specifications.
Furthermore, the integration of Industry 4.0 technologies, such as IoT sensors and data analytics, brings a new level of intelligence to the operation of high-efficiency ERW tube mills. Manufacturers can track performance metrics in real time, identify areas for improvement, and optimize maintenance schedules. This predictive maintenance capability minimizes potential downtime, ultimately enhancing productivity and profitability.
Challenges such as supply chain disruptions, fluctuating raw material costs, and increasing global competition compel manufacturers to seek innovative solutions. High-efficiency ERW tube mills address many of these challenges by improving resource utilization and offering flexible production schedules.
As businesses reap the benefits of high-efficiency ERW tube mills, industry stakeholders should recognize this technology's transformative potential. It serves as a catalyst for change, driving the modernization of processes and setting new benchmarks for quality and efficiency. As economic pressures and environmental imperatives continue to shape the manufacturing landscape, embracing high-efficiency ERW tube mill technology may well be a key factor for success and sustainability in the metalworking industry.
In conclusion, high-efficiency ERW tube mills exemplify how innovation in manufacturing technology can lead to enhanced productivity, reduced costs, and improved product quality. With their ability to adapt to changing market needs and drive sustainable practices, these mills are not just an asset for manufacturers—they are essential tools for future-readiness in a constantly evolving sector.