[Spare parts for Solid state HF welder]Essential Spare Parts for Solid State HF Welder: A Comprehensive Guide to Maintaining Optimal Performance and Longevity
News 2024-9-14
Solid State High Frequency (HF) Welders are an essential tool in various industrial applications, particularly in the fields of plastic welding, metal joining, and advanced manufacturing processes. These sophisticated machines utilize solid-state technology to produce high-frequency electrical currents that enable precise welding without the need for extensive heat or external pressure. Like all equipment, solid state HF welders require regular maintenance and sometimes replacement of components to ensure their optimal performance. One critical aspect of this maintenance is having access to spare parts. This article delves into the importance of spare parts for solid state HF welders, the common components that may need replacement, and tips for selecting and sourcing these essential items.
Importance of Spare Parts
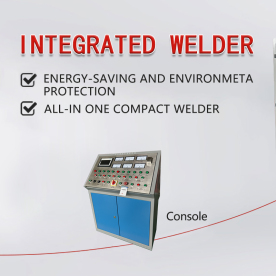
Essential Spare Parts for Solid State HF Welder: A Comprehensive Guide to Maintaining Optimal Performance and Longevity
Common Spare Parts for Solid State HF Welders
1. **Oscillators**: The oscillation circuit is a vital component in any solid state HF welder, responsible for generating high-frequency currents required for the welding process. If the oscillator fails, the welder may not operate at all, making the availability of an oscillator as a spare part essential for maintaining productivity.
2. **Transformers**: Transformers in solid state HF welders play a crucial role in voltage regulation. They convert the high-frequency signals into usable power levels. A faulty transformer can lead to inconsistent welding results or total machine failure, underscoring the necessity of having a replacement transformer on hand.
3. **Diodes**: Diodes are essential for controlling electrical current flow in a welder. Over time, diodes may degrade or fail, which can impact the efficiency of the welding process. Having spare diodes readily available can minimize disruptions during production runs.
4. **Capacitors**: Capacitors store electrical energy and release it when needed for the welding process. Age-related degradation can affect their performance, leading to inconsistent weld quality. Replacing capacitors as needed helps maintain the integrity of the welding operations.

Essential Spare Parts for Solid State HF Welder: A Comprehensive Guide to Maintaining Optimal Performance and Longevity
6. **Control Boards and Displays**: Modern HF welders come equipped with sophisticated control boards and digital displays that guide operators through the welding process. If these components fail, it can lead to operational confusion or incorrect settings. Having spare control boards can keep your welder functional and user-friendly.

Essential Spare Parts for Solid State HF Welder: A Comprehensive Guide to Maintaining Optimal Performance and Longevity
1. **Manufacturer Recommendations**: Always refer to the manufacturer’s specifications when looking for spare parts. They often provide a list of compatible parts and their part numbers, ensuring that you acquire the correct components.
2. **OEM vs. Aftermarket Parts**: Consider whether you want Original Equipment Manufacturer (OEM) parts or aftermarket alternatives. While OEM parts are typically more expensive, they ensure compatibility and reliability. Aftermarket parts may be less costly but can vary in quality.
3. **Use Reputable Suppliers**: Building relationships with reputable suppliers can facilitate efficient sourcing. Look for suppliers well-reviewed within the industry to ensure they provide quality parts and reliable service.
4. **Inventory Management**: Maintain a well-organized inventory of spare parts. Regularly assess the usage and condition of each component, so you can proactively replace parts before they fail.
5. **Regular Maintenance Checks**: Routine inspections can help identify wear and potential issues before they lead to equipment failure. During these checks, document which parts may need replacing soon, allowing you to plan orders conveniently.
In summary, having access to spare parts for solid state HF welders is critical for ensuring their effective operation and longevity. By understanding which components commonly require replacement and employing smart sourcing strategies, companies can minimize downtime, reduce repair costs, and maintain peak performance in their welding operations. Regular maintenance, proactive inspections, and a solid inventory of spare components will significantly contribute to the productive and efficient use of solid state HF welders in various industrial applications.