[Tube making machine for industrial applications]Revolutionizing Manufacturing Efficiency: The Role of Tube Making Machines for Industrial Applications
News 2024-9-13
****In today's fast-paced industrial landscape, the need for efficient and reliable manufacturing processes is more critical than ever. Among the various types of machinery that contribute to advanced manufacturing capabilities, tube making machines stand out as invaluable assets for businesses across multiple sectors. These machines are not only integral in producing high-quality tubing products; they also enhance productivity, reduce material waste, and support innovative design processes.
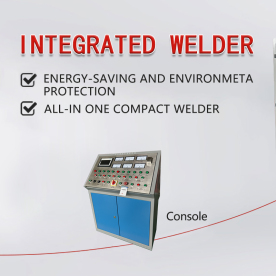
Revolutionizing Manufacturing Efficiency: The Role of Tube Making Machines for Industrial Applications
Types of Tube Making Machines
The types of tube making machines available today vary greatly based on design, functionality, and the materials they can process. Some of the most common types include:
1. **Welded Tube Making Machines:** These machines produce tubes by forming flat sheets of metal into a cylindrical shape and then welding the edges together. The welded tube method is prevalent because it allows for higher production rates and is commonly used for steel, stainless steel, and aluminum tubes.
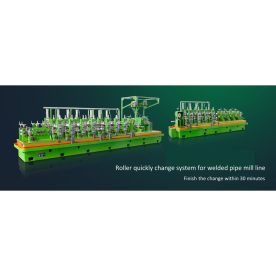
Revolutionizing Manufacturing Efficiency: The Role of Tube Making Machines for Industrial Applications

Revolutionizing Manufacturing Efficiency: The Role of Tube Making Machines for Industrial Applications
3. **Cold Drawn Tube Making Machines:** Cold drawing is a process that reduces the diameter and increases the length of a tube while also improving its yield strength. Cold drawn tube making machines are essential in industries that require precision-engineered tubes, such as medical instrumentation and aerospace components.
4. **Specialty Tube Making Machines:** These machines are designed for specific applications, producing tubes with unique shapes, dimensions, or material properties. Industries like automotive and advanced manufacturing often rely on specialty machines to create customized components that meet stringent regulatory and performance standards.
Applications of Tube Making Machines
The versatility of tube making machines makes them ubiquitous across various industries. Their applications can be observed in several fields:
- **Construction:** Steel and aluminum tubes produced by tube making machines are fundamental to the construction industry, providing structural support and critical framework in buildings and bridges.
- **Automotive:** The automotive sector relies heavily on tubes for exhaust systems, fuel lines, and structural components. Tube making machines enable manufacturers to produce tubes that meet rigorous safety and efficiency standards.
- **Aerospace:** Aerospace applications demand high precision and reliability. Seamless and cold drawn tubes are essential for fuel systems, hydraulic lines, and other applications where performance and strength are paramount.
- **Medical Devices:** The medical industry employs tubes in devices such as catheters and surgical instruments. Tube making machines can produce small, precision tubes that meet stringent hygienic and production standards.
Operational Benefits of Modern Tube Making Machines
Investing in modern tube making machinery yields a host of operational benefits. Here are some key advantages:
1. **Increased Production Speed:** Advanced tube making machines operate with high efficiency, reducing cycle times and increasing throughput.
2. **Enhanced Quality Control:** Sophisticated machinery equipped with automation and monitoring systems ensures that tubes produced meet exact specifications, minimizing defects and ensuring consistent quality.
3. **Reduced Material Waste:** Modern tube making machines are designed to optimize material usage, translating to less waste and more efficient production processes.
4. **Adaptability:** Many tube making machines can be adjusted for different tube sizes and materials, allowing manufacturers to pivot quickly in response to market demands or custom orders.
5. **Cost-Effectiveness:** The initial investment in tube making machines can be offset by reduced labor costs and improved production efficiency, ultimately leading to higher profit margins.
Future Trends in Tube Making Technology
As industries continue to evolve, tube making machines will undoubtedly adapt to meet new challenges. The integration of smart technology, artificial intelligence, and automation into manufacturing processes is likely to provide even greater efficiencies. Additionally, the growing emphasis on sustainability could drive innovations in tube making materials and processes to reduce environmental impacts.
In conclusion, tube making machines are a cornerstone technology in industrial applications, serving diverse sectors with innovative solutions that enhance productivity and quality. As technology progresses, manufacturers must remain vigilant in adopting these advancements to maintain competitiveness and drive future growth. Investing in state-of-the-art tube making machinery will not only help businesses stay ahead of the curve but also create a foundation for sustainable success in an ever-evolving market.