[Advanced Tube making machinery]Exploring the Innovation and Efficiency of Advanced Tube Making Machinery in Modern Manufacturing Processes
News 2024-9-10
****In the landscape of modern manufacturing, the production of tubes has become a critical component across various industries, from construction and automotive to aerospace and medical applications. As the demand for high-quality, precision-engineered tubes continues to escalate, the importance of Advanced Tube Making Machinery has never been more pronounced. This technology not only enhances productivity but also ensures that manufacturers can meet the stringent standards required in today's competitive marketplace.
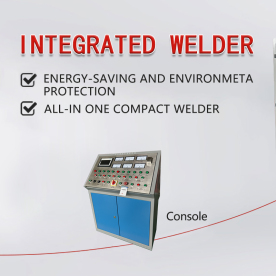
Exploring the Innovation and Efficiency of Advanced Tube Making Machinery in Modern Manufacturing Processes
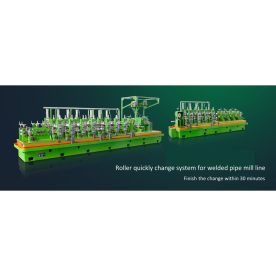
Exploring the Innovation and Efficiency of Advanced Tube Making Machinery in Modern Manufacturing Processes
Advanced tube making machinery comprises a range of sophisticated equipment designed for the efficient production of tubes made from various materials, including metals, plastics, and composites. These machines utilize cutting-edge technologies such as automation, robotics, and computer numerical control (CNC) to produce tubes that meet specific dimensions, tolerances, and mechanical properties.
The key components of this machinery often include tube forming machines, welding equipment, tube finishing tools, and quality inspection systems. Each of these elements plays a vital role in ensuring the functionality and reliability of the final product. For instance, tube forming machines use processes such as bending, drawing, and extrusion to shape the raw material into the desired tube configuration. Welding equipment is crucial for creating long, continuous tubes from shorter sections, while finishing tools ensure that the tube's surface meets industry standards for smoothness and durability.
Benefits of Implementing Advanced Tube Making Technology
One of the primary advantages of using Advanced Tube Making Machinery is the significant increase in production efficiency. Automated systems can operate at high speeds, reducing cycle times and allowing manufacturers to produce greater quantities of product in a shorter period. This is particularly important in industries where time-to-market is essential and where delays can lead to lost contracts and revenue.
Moreover, advanced machinery offers improved precision and consistency. Manual tube production methods often lead to variability in product quality, which can be costly for manufacturers in terms of rework and warranty claims. Advanced machinery, equipped with precise programming and sensors, minimizes human error, ensuring that each tube is produced to the exact specifications required by clients.

Exploring the Innovation and Efficiency of Advanced Tube Making Machinery in Modern Manufacturing Processes
Environmental Considerations
With growing awareness of environmental issues, manufacturers today are increasingly focused on sustainability. Advanced tube making machinery can contribute significantly to reducing the environmental impact of production processes. Modern machines are designed to minimize energy consumption and waste generation. Additionally, the ability to use recycled materials in tube production is enhanced with advanced equipment, as it often accommodates a broader range of feedstock, including secondary raw materials.
Challenges and Future Trends
Despite its many benefits, the adoption of Advanced Tube Making Machinery is not without its challenges. The high cost of purchasing and maintaining sophisticated equipment is a significant barrier for some manufacturers, especially smaller businesses. Additionally, the rapid pace of technological advancement means that ongoing training and investment in workforce development are crucial. Companies must ensure that their employees are skilled in operating and maintaining advanced machinery to maximize returns on their investment.
Looking forward, the future of tube production will likely see continued integration of smart technologies, such as the Internet of Things (IoT), artificial intelligence (AI), and machine learning. These innovations can further enhance the efficiency and flexibility of tube manufacturing processes, enabling manufacturers to adapt quickly to changing market demands and customer preferences.
Conclusion
In conclusion, Advanced Tube Making Machinery offers a host of benefits that can significantly improve the efficiency, quality, and environmental sustainability of tube production. As industries continue to evolve and face new challenges, the adoption of these advanced technologies will be essential for manufacturers seeking to maintain a competitive edge. Embracing these innovations not only enhances operational efficiency but also positions businesses to respond more effectively to the ever-changing demands of the global marketplace.