[Automatic high frequency welder]Understanding the Advantages and Applications of Automatic High Frequency Welders in Modern Manufacturing Processes
News 2024-9-9
In the world of manufacturing, especially in applications involving metals, the efficiency and quality of joining processes are critical. Among these processes, welding stands out as one of the most essential techniques. One of the most innovative advancements in welding technology is the Automatic High Frequency Welder. This type of welder has revolutionized various industries by enhancing efficiency, reducing production time, and delivering superior weld quality. This article explores the working mechanism, advantages, applications, and future of automatic high-frequency welders.
What is an Automatic High Frequency Welder?
An Automatic High Frequency Welder is a specialized machine designed to produce high-quality welds through the application of high-frequency electrical currents. It is commonly used for welding thin-walled metals, such as tubes and pipes, and for various applications in the automotive, aerospace, and construction industries. The operation involves generating high-frequency electromagnetic fields that cause metal surfaces to heat up rapidly, facilitating the fusing of materials without the need for extensive filler materials or external heat sources.
How Do Automatic High Frequency Welders Work?
The operation of an automatic high-frequency welder can be broken down into several key stages:
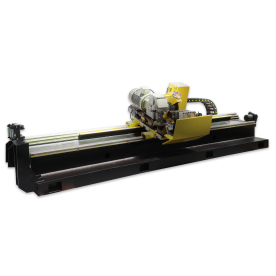
Understanding the Advantages and Applications of Automatic High Frequency Welders in Modern Manufacturing Processes
2. **Application of High-Frequency Energy**: Once the materials are in place, the machine generates high-frequency electrical currents, typically in the range of several hundred kHz to MHz. These currents create an electromagnetic field around the welding area.
3. **Heating the Workpieces**: The electromagnetic field induces heat in the metal components due to resistance. This quickly raises the temperature of the workpieces near the joint.
4. **Joining the Materials**: Once the required temperature is achieved, the automatic welder applies pressure to the workpieces. The combination of heat and pressure yields a strong joint as the surfaces fuse together.
5. **Cooling Process**: After the weld is formed, the automatic welder often includes mechanisms to manage cooling, ensuring that the weld solidifies uniformly and retains its structural integrity.
Advantages of Using Automatic High Frequency Welders
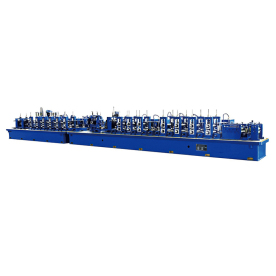
Understanding the Advantages and Applications of Automatic High Frequency Welders in Modern Manufacturing Processes
2. **Consistent Quality**: Automatic welders offer higher consistency in weld quality due to their pre-configured settings and automated precision. This lowers the chances of human error and variability, resulting in reliable production outcomes.
3. **Reduced Material Waste**: The high precision of automatic welders minimizes the need for filler materials, reducing both cost and material waste. This efficiency is particularly beneficial in industries with strict environmental regulations.
4. **Safety Improvements**: By automating the welding process, human exposure to hazardous conditions is significantly reduced. Moreover, automatic high-frequency welders are designed with safety features to protect operators from exposure to high voltage and heat.
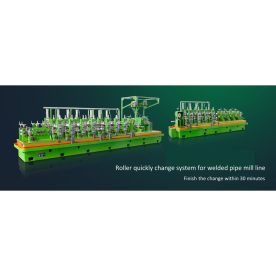
Understanding the Advantages and Applications of Automatic High Frequency Welders in Modern Manufacturing Processes
Applications of Automatic High Frequency Welders
Automatic high-frequency welders are widely used across several industries:
- **Automotive Industry**: They are employed in producing exhaust systems, fuel tanks, and structural components where strong and lightweight welds are necessary. - **Aerospace Industry**: For aerospace applications, the precision and strength of the welds are critical due to the high standards for safety and performance.
- **Construction**: In construction, these welders are used for fabricating steel tubes, handrails, and metal structures that require swift and dependable welding solutions.
- **Manufacturing of Electrical Components**: High-frequency welders are also used for assembling components like transformers and induction coils, where material specifications demand exact welding techniques.
The Future of Automatic High Frequency Welders
As industries continue to evolve with the introduction of smart manufacturing and automation, the importance of advanced welding systems like automatic high-frequency welders will only grow. Future innovations may focus on improving energy efficiency, achieving even greater precision, and integrating advanced monitoring systems that can provide real-time data on weld quality and process efficiency.
In conclusion, the Automatic High Frequency Welder stands as a testament to the advancements in welding technology. By enhancing speed, quality, and safety, these machines are paving the way for more efficient manufacturing processes across many sectors. As technology continues to develop, the role of automatic high-frequency welders will undoubtedly become more integral in achieving production goals and meeting industry demands.