[All-in-one High Frequency Welder for Metal Processing]Revolutionizing Industrial Metal Fabrication: The All-in-One High Frequency Welder for Metal Processing
News 2024-9-6
****In today’s fast-paced manufacturing and metalworking environment, efficiency and versatility are paramount. Traditional welding methods often come with limitations, leading professionals to seek innovative solutions that enhance productivity while maintaining high standards of quality. One such solution that has gained significant traction is the All-in-One High Frequency Welder for Metal Processing. This cutting-edge tool combines multiple functionalities, ensuring that fabricators can achieve optimal results across a variety of applications.
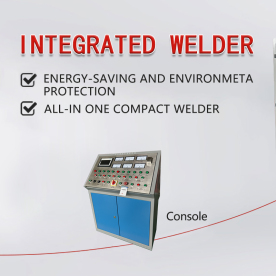
Revolutionizing Industrial Metal Fabrication: The All-in-One High Frequency Welder for Metal Processing
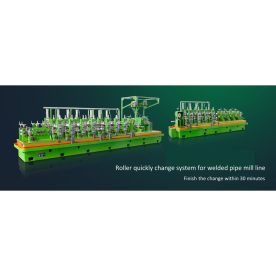
Revolutionizing Industrial Metal Fabrication: The All-in-One High Frequency Welder for Metal Processing
Features of an All-in-One High Frequency Welder
The term "All-in-One" refers to the multifunctional nature of the welder, meaning it can perform a wide range of welding processes — including high frequency, TIG, MIG, and spot welding — all with a single machine. This versatility is incredibly beneficial for metal fabrication shops that need to adapt to diverse projects without investing in separate equipment for each welding method.
1. **Compact Design**: The All-in-One High Frequency Welder typically has a space-saving design, making it ideal for workshops with limited space. Despite its compactness, it does not compromise on power or performance.
2. **User-Friendly Interface**: Modern welding machines come equipped with intuitive controls and digital displays that enable operators to adjust settings with ease. This accessibility not only speeds up the learning curve for new operators but also helps experienced users achieve their desired results more efficiently.
3. **Integrated Safety Features**: Safety is, of course, a primary concern in any welding operation. High frequency welders come with built-in safety protocols such as automatic shut-off, thermal overload protection, and adequate shielding to protect the operator from excessive UV exposure.

Revolutionizing Industrial Metal Fabrication: The All-in-One High Frequency Welder for Metal Processing
5. **Energy Efficiency**: As the global focus shifts towards sustainable practices, the energy efficiency of welding equipment becomes more important than ever. Many modern high frequency welders optimize energy consumption, reducing operational costs while minimizing environmental impact.
Advantages for Metal Processing
**Enhanced Productivity**: With the ability to switch between multiple welding processes seamlessly, fabricators can execute a higher volume of work in shorter timeframes. The reduced waiting time for warm-up and setup leads to greater efficiency, minimizing downtime.
**Improved Weld Quality**: The precision offered by high frequency welding minimizes the likelihood of defects such as porosity or lack of penetration, which can occur with traditional welding techniques. The resulting strong joints meet or exceed the expectations of engineers and designers alike.
**Cost-Effectiveness**: By consolidating multiple machines into one, businesses can significantly lower their capital investment. The operational savings, combined with minimized repair and maintenance costs, enhance overall profitability.
Conclusion
As the metal processing industry continues to evolve, investing in innovative solutions like the All-in-One High Frequency Welder becomes increasingly essential. The combination of versatility, efficiency, and advanced technology makes it a game-changer for metal fabrication businesses. Adopting such state-of-the-art equipment not only streamlines operations but also positions companies to better meet the ever-changing demands of the industry.
In conclusion, for those seeking to elevate their metal processing capabilities, an All-in-One High Frequency Welder represents not just an investment in machinery but in the future of welding technology. By embracing this advanced solution, fabricators can place themselves at the forefront of the industry, equipped to tackle even the most challenging projects with confidence and precision.