[High-precision tube making machine ]Exploring the Advanced Capabilities and Benefits of High-Precision Tube Making Machines in Modern Manufacturing
News 2024-9-6
In the rapidly evolving landscape of manufacturing technology, precision and efficiency are paramount. High-precision tube making machines play a vital role in various industries, including automotive, aerospace, medical, and construction. These machines are engineered to create tubes of exceptional accuracy and quality, meeting the stringent demands of modern production environments. This article delves into the intricacies of high-precision tube making machines, highlighting their technological features, benefits, and applications across different sectors.
Understanding High-Precision Tube Making Machines
High-precision tube making machines are specialized equipment designed for the production of precision tubes. They utilize advanced manufacturing processes involving CNC (Computer Numerical Control) technology, automation, and sophisticated software to ensure the highest level of accuracy. These machines can produce tubes from a wide range of materials, including metals, plastics, and composites, with diameters as small as a few millimeters to large sections exceeding several inches.
One of the most significant advancements in high-precision tube making machines is their ability to maintain tight tolerances. Tolerances are critical in applications where tubes must fit seamlessly with other components, such as in hydraulic systems, medical devices, and structural applications. Some state-of-the-art machines can achieve tolerances as tight as ±0.01 mm, which is crucial for ensuring the overall performance and safety of the final product.
Key Features of High-Precision Tube Making Machines
1. **CNC Technology**: Modern tube making machines are predominantly CNC-controlled, allowing for highly automated operations. This results in consistent product quality, reduced waste, and lower labor costs.
2. **Versatile Material Handling**: High-precision tube making machines can handle a variety of materials, including stainless steel, aluminum, copper, and specialized alloys. The ability to work with different materials expands their applicability across various industries.
3. **Customizable Production Settings**: Operators can easily customize the machine settings according to specific production requirements. This includes adjusting speed, temperature, and tension based on the material and desired end product.
4. **Integrated Quality Control**: Many high-precision tube making machines come with integrated quality control systems that monitor the production process in real-time. This feature ensures that any deviations from specified tolerances are identified and corrected immediately.
5. **Environmentally Friendly**: Modern machines are designed with energy efficiency in mind. They employ technologies that reduce waste and lower energy consumption, aligning with global sustainability goals.
Benefits of High-Precision Tube Making Machines
1. **Enhanced Productivity**: The high-speed capabilities and automation features of these machines result in increased production rates. Manufacturers can produce larger quantities of tubes in a shorter duration, meeting market demands more effectively.
2. **Cost-Effective Manufacturing**: Although the initial investment in high-precision tube making machines can be significant, their long-term savings in material usage, labor costs, and reduced error rates contribute to overall cost-effectiveness.
3. **Improved Product Quality**: The precision capabilities of these machines minimize defects and inconsistencies, leading to higher quality finished products. This level of quality is particularly critical in industries where precision is essential for safety and performance.
4. **Flexibility in Production**: High-precision tube making machines can be programmed to produce various tube sizes and types, enabling manufacturers to pivot quickly based on changing customer demands or market trends.
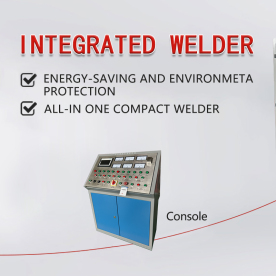
Exploring the Advanced Capabilities and Benefits of High-Precision Tube Making Machines in Modern Manufacturing
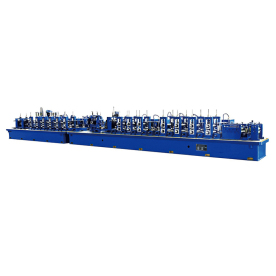
Exploring the Advanced Capabilities and Benefits of High-Precision Tube Making Machines in Modern Manufacturing
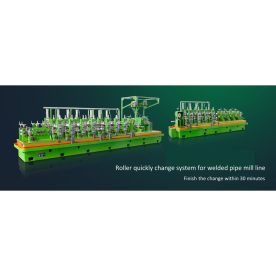
Exploring the Advanced Capabilities and Benefits of High-Precision Tube Making Machines in Modern Manufacturing
- **Automotive**: Production of fuel lines, exhaust systems, and structural components that require high-performance specifications. - **Aerospace**: Fabrication of lightweight yet durable tubes for fuel systems and hydraulic lines in aircraft. - **Medical**: Creation of precision tubes for medical devices, including catheters and syringes, where accuracy and hygiene are critical. - **Construction**: Manufacturing of tubes used in scaffolding, piping, and support structures.
Conclusion
High-precision tube making machines represent a significant leap in manufacturing technology, providing unparalleled accuracy, efficiency, and flexibility. As industries continue to demand higher quality and lower production costs, the adoption of these machines is expected to grow. Embracing the capabilities of high-precision tube making machines not only enhances production processes but also paves the way for innovation in product design and manufacturing techniques across various sectors. With their proven benefits and expanding applications, these machines are poised to play a crucial role in the future of manufacturing.