[Automatic ERW tube mill equipment]Exploring the Advantages and Innovations of Automatic ERW Tube Mill Equipment in Modern Manufacturing Processes
News 2024-9-6
The manufacturing industry has seen tremendous advancements in technology over the years, leading to more efficient and precise production methods. One such development is the Automatic ERW (Electric Resistance Welding) tube mill equipment, which has revolutionized the way tubular products are manufactured. This cutting-edge technology has enabled manufacturers to enhance productivity while maintaining high-quality standards. In this article, we will explore the workings, advantages, and innovations surrounding Automatic ERW tube mill equipment.
Understanding Automatic ERW Tube Mill Equipment
Automatic ERW tube mills are state-of-the-art machines specifically designed for the manufacturing of steel tubes and pipes through the electric resistance welding process. The technology uses electric current to heat the edges of steel strips, creating a weld as the material is formed into a tube. The automatic nature of these mills means that processes are controlled through sophisticated software that monitors variables such as temperature, pressure, and feed speed in real time, minimizing human error and maximizing productivity.
These mills typically consist of several major components, including a decoiler, forming machine, welding equipment, sizing section, and cutting station. Each component plays a crucial role in the tube production process, from unrolling the steel coil to the final cutting of the finished tube to the desired length. Advanced Automatic ERW tube mills are often equipped with in-line testing and inspection systems, ensuring that the final product meets stringent quality standards before being dispatched.
Advantages of Automatic ERW Tube Mill Equipment
1. **High Production Efficiency**: The automation of processes allows for continuous operation, thereby significantly increasing the production rate. Manufacturers can produce a larger volume of tubes in a shorter time frame, reducing lead times and increasing overall output.
2. **Consistent Quality Control**: Automatic ERW tube mills utilize advanced monitoring technology, which helps maintain uniformity in the manufacturing process. Real-time data collection allows for immediate adjustments to be made, ensuring that the final product adheres to strict specifications.
3. **Reduced Labor Costs**: With automation in place, the dependence on manual labor is greatly decreased. Fewer employees are required to operate and monitor the machines, allowing manufacturers to allocate resources to other areas of their operations, which can lead to cost savings.
4. **Flexibility in Production**: Modern Automatic ERW tube mills can be easily reconfigured to produce various tube sizes and shapes. This flexibility enables manufacturers to quickly adapt to market demands or specific client requests, enhancing their competitiveness.
5. **Improved Safety**: Automated systems often incorporate safety features that reduce the chances of accidents on the factory floor. By minimizing human intervention in potentially hazardous processes, the safety of workers is enhanced.
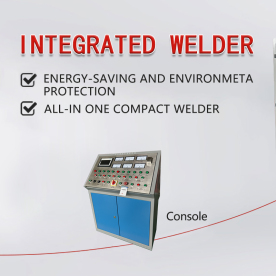
Exploring the Advantages and Innovations of Automatic ERW Tube Mill Equipment in Modern Manufacturing Processes
Innovations in Automatic ERW Tube Mill Technology
Recent innovations in Automatic ERW tube mill equipment have led to even more enhancements in performance and capabilities. For instance, the integration of Industry 4.0 principles has paved the way for smart factories, wherein machines communicate with each other and with central systems. This connectivity allows for predictive maintenance, which can identify potential issues before they cause breakdowns, thus further minimizing downtime and production disruptions.
Moreover, advancements in artificial intelligence and machine learning algorithms enable these mills to optimize their operations continuously. By analyzing patterns in production data, these AI-driven systems can suggest adjustments to processes, leading to better quality control and resource management.
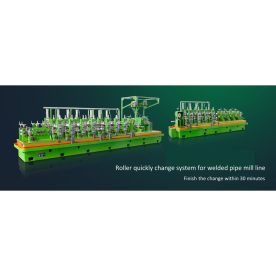
Exploring the Advantages and Innovations of Automatic ERW Tube Mill Equipment in Modern Manufacturing Processes

Exploring the Advantages and Innovations of Automatic ERW Tube Mill Equipment in Modern Manufacturing Processes
Conclusion
Automatic ERW tube mill equipment stands as a testament to the remarkable progress of industrial manufacturing technology. Its ability to enhance productivity, ensure consistent quality, and reduce operational costs makes it a crucial asset for manufacturers in today's competitive market. As innovations continue to emerge, the capabilities of these mills are expected to evolve, further solidifying their role in the future of manufacturing. Embracing this technology not only streamlines operations but also positions manufacturers to meet the growing demands of the global economy efficiently.