[IF pipe seam annealing machine ]Revolutionizing Pipe Manufacturing: The Integral Role of IF Pipe Seam Annealing Machines in Enhancing Weld Quality and Production Efficiency
News 2024-9-5
In the ever-evolving landscape of pipe manufacturing, technology has played a pivotal role in enhancing product quality and operational efficiency. One of the key innovations driving this transformation is the IF pipe seam annealing machine. Designed to treat welded seams on pipes, this equipment has become essential in industries such as oil and gas, water supply, and structural applications. Understanding what an IF pipe seam annealing machine is, how it operates, and its benefits can provide manufacturers with significant advantages in today’s competitive market.
Understanding IF Pipe Seam Annealing Machines
Intermittent Furnacing (IF) pipe seam annealing machines are specialized equipment that subject welded pipes to controlled heating followed by cooling. This process aims to restore the material properties of the weld joint, which can be adversely affected during the welding process. The IF method is characterized by its ability to deliver consistent heat across the entire length of the welded seam without affecting the integrity of the surrounding material.
The process begins with the pipe being fed into the annealing machine, where it is heated to a specified temperature. The duration and temperature of annealing can vary based on the type of materials used and the desired properties of the finished product. After heating, the pipes are cooled, typically through air cooling or forced air, to enhance material strength and ductility.
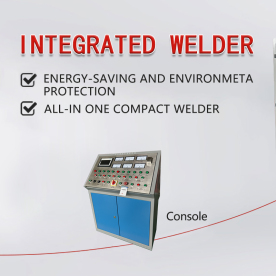
Revolutionizing Pipe Manufacturing: The Integral Role of IF Pipe Seam Annealing Machines in Enhancing Weld Quality and Production Efficiency
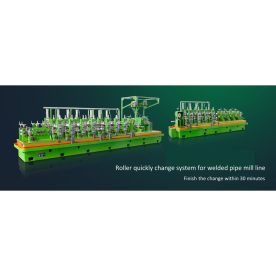
Revolutionizing Pipe Manufacturing: The Integral Role of IF Pipe Seam Annealing Machines in Enhancing Weld Quality and Production Efficiency

Revolutionizing Pipe Manufacturing: The Integral Role of IF Pipe Seam Annealing Machines in Enhancing Weld Quality and Production Efficiency
By utilizing an IF pipe seam annealing machine, manufacturers can significantly improve the quality of their welded pipes. Benefits include:
1. **Enhanced Mechanical Properties**: The annealing process helps in restoring the original mechanical properties of the pipe material. This leads to improved toughness and corrosion resistance, making the pipes more suitable for high-pressure applications.
2. **Reduced Risk of Defects**: Pipes that undergo proper annealing show a lower incidence of defects such as cracks and inclusions. The uniform heating and controlled cooling ensure that the welds are consistent, reducing the risk of failure in the final product.
3. **Cost-Effectiveness**: An IF pipe seam annealing machine can lead to significant cost savings. By improving the quality and consistency of the pipes, manufacturers can reduce waste, minimize rework, and enhance customer satisfaction by delivering high-quality products.
Operational Efficiency and Technological Advancements
The advancement of technology in the design and operation of IF pipe seam annealing machines has contributed to improved efficiency. Modern machines are equipped with sophisticated control systems that monitor temperature and cooling rates in real-time. This automation minimizes human error and ensures that the annealing process is maintained within optimal parameters.
Moreover, energy efficiency is a critical consideration in manufacturing. Many contemporary IF pipe seam annealing machines are designed to reduce energy consumption through the use of insulation, waste heat recovery systems, and advanced heating technologies. This not only supports sustainability efforts but also contributes to lower operational costs.
Conclusion
The IF pipe seam annealing machine has become an indispensable component in the modern pipe manufacturing process. By enhancing the quality of welded seams and improving material properties, it offers manufacturers a pathway to produce superior products that meet the stringent demands of various industries. As technology continues to advance, the capabilities of these machines will likely expand further, making them even more integral to achieving operational excellence in pipe production. By investing in IF pipe seam annealing technology, manufacturers are not just keeping up with industry standards but are also setting new benchmarks for quality and efficiency in the market.