[Precision Tube making equipment]Explore the Essential Role of Precision Tube Making Equipment in Modern Manufacturing: Enhancing Efficiency and Quality in the Production Process
News 2024-9-5
In today’s fast-paced manufacturing environment, precision is paramount. Industries ranging from automotive to aerospace rely on components that meet stringent specifications and tolerances. To achieve such levels of precision, manufacturers need advanced tools and machines that can produce high-quality results consistently. One such tool that has become indispensable in these processes is precision tube making equipment.
Precision tube making equipment encompasses a variety of machines and technologies designed to fabricate tubes with exacting specifications. These devices are utilized to create tubes from various materials including metals, plastics, and composites, all tailored to meet the diverse needs of different industries. The production of tubes requires not only accurate measurements but also advanced techniques that can handle specific material properties and the intricacies of various applications.
The Importance of Precision in Tube Manufacturing
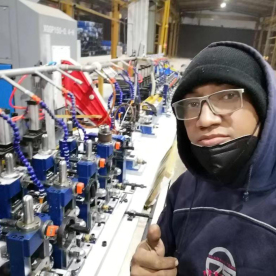
Explore the Essential Role of Precision Tube Making Equipment in Modern Manufacturing: Enhancing Efficiency and Quality in the Production Process
Types of Precision Tube Making Equipment
The realm of precision tube making includes several different types of machinery, each suited for specific tasks.
1. **Tube Cutting Machines**: The first step in tube production often involves cutting raw materials into smaller segments. Precision tube cutting machines can quickly and accurately cut materials to length with minimal waste. These machines use various techniques, including saw cutting, laser cutting, and water jet cutting, to achieve the required specifications.
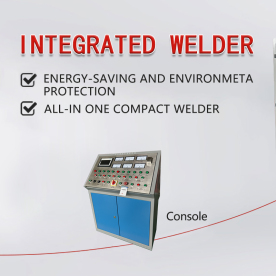
Explore the Essential Role of Precision Tube Making Equipment in Modern Manufacturing: Enhancing Efficiency and Quality in the Production Process
3. **Tube Forming Machines**: Tube forming processes may include notching, flaring, or expanding. Precision tube forming equipment uses specialized dies to shape the tube according to exact designs. These processes are particularly important in industries where tubes need to fit into complex assemblies or require additional features for functionality.
4. **Welding and Joining Equipment**: In many cases, sections of tubular material need to be joined together. High-quality welding equipment designed specifically for precision tube making allows for strong, reliable joints. Techniques like TIG (Tungsten Inert Gas) welding provide the precision required for critical applications in industries such as aerospace and medical technologies.
5. **Inspection and Testing Machines**: No production process is complete without rigorous testing. Precision inspection equipment ensures that the produced tubes meet all specified dimensions and tolerances. Advanced measurement techniques such as laser scanning or coordinate measuring machines (CMM) are often employed to verify accuracy.
Benefits of Precision Tube Making Equipment
Investing in precision tube making equipment offers numerous benefits. First and foremost, it increases efficiency. Automated machines reduce the time and labor required for production, allowing for higher output rates. Additionally, these machines often require less manual adjustment, further enhancing operational efficiency.
Quality improvement is another significant advantage. Precision equipment reduces the likelihood of defects, ensuring that each tube meets industry standards and customer expectations. Enhanced quality also translates to reduced scrap rates, making production processes more cost-effective.
Moreover, the versatility of precision tube making equipment allows manufacturers to adjust to varying market demands. As industries evolve, the need for custom solutions increases. Advanced tube making machines can accommodate a wide range of materials and specifications, making them adaptable to different project requirements.
Conclusion
