[Tube making machine for industrial applications]Exploring the Versatility and Efficiency of Tube Making Machines for Diverse Industrial Applications
News 2024-9-4
In today’s fast-paced industrial landscape, the demand for precision-engineered products is greater than ever. Industries ranging from automotive to aerospace, construction to medical, require high-quality tubes and pipes that meet strict specifications. One of the pivotal developments in this realm is the tube making machine, a hallmark of modern manufacturing that ensures efficiency, precision, and versatility across various applications. This article delves into the significance of tube making machines in industrial settings, highlighting their operations, benefits, and the variety of industries that leverage their capabilities.
Understanding Tube Making Machines
At their core, tube making machines are specialized equipment designed to manufacture tubes and pipes from a variety of raw materials, including metals, plastics, and composites. The production process typically involves several key stages: forming, welding, and finishing. During the forming stage, raw materials are shaped into a tubular profile; for metal tubes, this often involves processes such as roll forming or extrusion. Subsequently, these formed pieces are welded together to ensure structural integrity. Lastly, the tubes undergo a finishing process that may include cutting, bending, or treating surfaces to achieve desired specifications and properties.
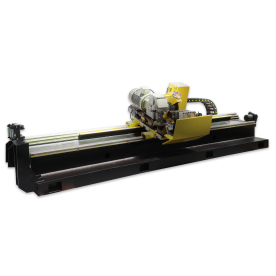
Exploring the Versatility and Efficiency of Tube Making Machines for Diverse Industrial Applications
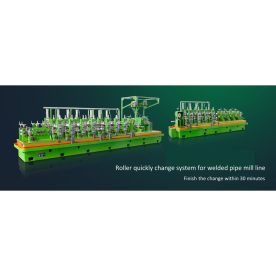
Exploring the Versatility and Efficiency of Tube Making Machines for Diverse Industrial Applications
2. **Precision**: In industries where tolerances are critical, tube making machines excel by offering unrivaled levels of precision. Advanced technologies, such as CNC (Computer Numerical Control) systems, allow for the creation of tubes with exact dimensions, promoting consistency and reducing waste.
3. **Versatility**: Tube making machines are adaptable to various materials and designs. Whether it is thin-walled tubes for medical applications or thick-walled pipes for structural purposes, these machines can be adjusted to accommodate different manufacturing requirements. Additionally, various types of finishes can be achieved, making them suitable for aesthetic applications as well.
4. **Quality Control**: Many modern tube making machines incorporate real-time monitoring systems that help ensure quality throughout the production process. These systems can detect anomalies or defects early on, allowing manufacturers to address issues promptly and maintain high standards.

Exploring the Versatility and Efficiency of Tube Making Machines for Diverse Industrial Applications
1. **Automotive**: The automotive industry utilizes tube making machines to produce essential components such as exhaust systems, structural tubing, and fuel lines. The ability to create lightweight yet durable tubes directly contributes to advancements in automotive design and fuel efficiency.
2. **Aerospace**: In aerospace applications, where weight and strength are crucial, tube making machines produce high-strength aluminum and titanium tubes. These materials are vital for components in aircraft and spacecraft, underscoring the importance of precision manufacturing.
3. **Medical**: The medical field benefits from tube making machines through the production of various medical devices. From slender tubes used in catheters to larger tubes for oxygen delivery systems, the precision and sterilization capabilities of these machines meet the stringent demands of medical applications.
4. **Construction**: The construction industry extensively uses tubes and pipes in structural frameworks, plumbing systems, and HVAC setups. Tube making machines enable fast and reliable production of these essential components, ensuring that buildings are safe, functional, and energy-efficient.
5. **Oil and Gas**: Steel and composite tubes are fundamental in the oil and gas sector for transporting fluids and gases. Tube making machines are crucial for manufacturing high-strength tubes capable of enduring extreme pressures and corrosive environments.
Future Trends and Innovations
As industries continue to evolve, so too do tube making machines. Innovations such as automation, artificial intelligence (AI), and Industry 4.0 technologies are transforming tube manufacturing. These advancements promise enhanced efficiency, predictive maintenance, and greater flexibility, allowing manufacturers to respond nimbly to changing market demands.
In conclusion, tube making machines are indispensable in a wide array of industrial applications, driving efficiency, precision, and adaptability in production processes. Their significance cannot be overstated as they contribute to advancements across various sectors, paving the way for future innovations and improvements in industrial manufacturing. As technology continues to advance, tube making machines will remain at the forefront of productive capabilities, shaping the future of industries worldwide.