[Heavy-Duty Cold Cutting Saw Machine]Exploring the Benefits and Applications of Heavy-Duty Cold Cutting Saw Machines in Precision Metal Processing and Fabrication
News 2024-9-3
In the industrial sector, the demand for precision and efficiency in metal cutting processes has never been more critical. As businesses strive to enhance productivity while maintaining high standards of quality, the Heavy-Duty Cold Cutting Saw Machine has emerged as an indispensable tool for metalworkers across various industries. This machinery not only ensures precise cuts but also offers numerous advantages over traditional cutting methods, including reduced operational costs and improved safety.
Understanding Heavy-Duty Cold Cutting Saw Machines
At its core, a Heavy-Duty Cold Cutting Saw Machine is designed to perform cutting processes on a wide range of metals, including steel, aluminum, and more. Unlike traditional saws that generate significant heat during operation, cold cutting saws utilize a circular blade made from high-speed steel (HSS) or carbide, which minimizes heat generation. This feature is crucial, as excessive heat can warp the material, affect the integrity of the cut, and lead to poor material performance in its final application.
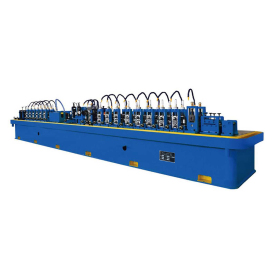
Exploring the Benefits and Applications of Heavy-Duty Cold Cutting Saw Machines in Precision Metal Processing and Fabrication
Key Features and Technologies
1. **Precision Cutting**: Heavy-Duty Cold Cutting Saw Machines are equipped with advanced technology that allows for highly accurate cuts. With features such as programmable settings and automatic feed, operators can achieve high tolerances, resulting in minimized waste and optimal end-product quality.
2. **Material Versatility**: These machines can handle diverse materials, making them suitable for various applications. Whether it’s cutting heavy metal pipes, solid bars, or sheets, the versatility of these saws ensures that they meet the needs of different projects efficiently.
3. **Enhanced Safety Features**: Safety is paramount in any industrial setting. Heavy-duty cold cutting saws come with numerous safety features, including blade guards, emergency stop buttons, and automatic shut-off mechanisms, ensuring a safer working environment for operators.
4. **Low Maintenance Requirements**: Built to operate in demanding conditions, these machines require minimal maintenance. Regular check-ups and proper handling can extend their longevity significantly, making them a sound investment for businesses.

Exploring the Benefits and Applications of Heavy-Duty Cold Cutting Saw Machines in Precision Metal Processing and Fabrication
**1. Construction**: In the construction industry, Heavy-Duty Cold Cutting Saw Machines play a vital role in fabricating structural steel components for buildings, bridges, and other infrastructure projects. Their ability to make clean cuts ensures the components fit together precisely during assembly.
**2. Manufacturing**: Manufacturing facilities utilize heavy-duty cold cutting saws for producing metal parts for machinery, automotive components, and consumer products. The precision cutting capabilities allow manufacturers to maintain consistent quality across large volumes of production.
**3. Aerospace**: The aerospace sector requires exceptionally precise machining to meet stringent safety and performance standards. Cold cutting saws help in producing lightweight and durable components that meet aviation regulations.
**4. Energy Sector**: In the energy sector, particularly in oil and gas, heavy-duty saws are used for cutting pipes and tubing that must withstand high pressures and temperatures. The cutting accuracy is crucial for ensuring the reliability of these materials in demanding environments.
Economic Advantages
Investing in Heavy-Duty Cold Cutting Saw Machines can significantly enhance a company's bottom line. The efficiency of these machines translates to reduced labor costs and shorter project timelines. Since the cutting process minimizes the need for additional finishing work, companies can allocate resources more effectively.
Moreover, the durability and low maintenance needs of these machines mean fewer downtimes and lower overall equipment costs. These economic factors contribute to a rapid return on investment (ROI) and foster business growth.
Conclusion
