[High-efficiency ERW tube mill]Exploring the Advancements and Benefits of High-Efficiency ERW Tube Mill Technology in Modern Manufacturing Processes
News 2024-9-3
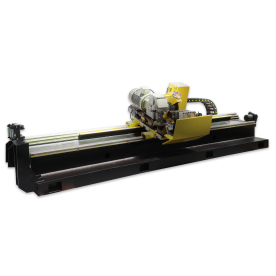
Exploring the Advancements and Benefits of High-Efficiency ERW Tube Mill Technology in Modern Manufacturing Processes
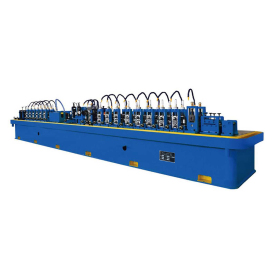
Exploring the Advancements and Benefits of High-Efficiency ERW Tube Mill Technology in Modern Manufacturing Processes
At its core, the ERW tube mill is designed to produce round, square, or rectangular tubes by utilizing the electric resistance welding technique. This process involves passing an electrical current through metal strips, which generates heat at the edges of the material, allowing it to be welded together as it is shaped into a tube. The high-efficiency variant of this machinery boasts enhanced performance metrics, including faster production speeds, reduced energy consumption, and improved weld quality.
One of the foremost benefits of high-efficiency ERW tube mills is their ability to produce tubes with extreme precision and uniformity. The machines are engineered with advanced control systems that ensure tight tolerances and consistent dimensions throughout the production process. This level of precision is crucial for industries where the slightest deviation can lead to significant failures, particularly in applications such as automotive and aerospace.
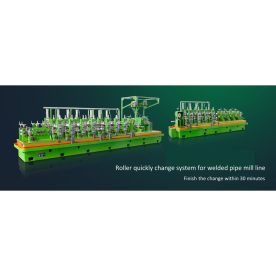
Exploring the Advancements and Benefits of High-Efficiency ERW Tube Mill Technology in Modern Manufacturing Processes
Energy efficiency is another hallmark of high-efficiency ERW tube mills. Traditional tube mills often consume considerable amounts of energy, which can be a major operational cost. However, modern high-efficiency models are designed to minimize energy usage while still delivering high performance. This is achieved through the use of energy-efficient components and smart production processes that significantly reduce waste and energy loss. Consequently, manufacturers can realize substantial savings on utility costs, and they also benefit from a more environmentally sustainable production process.
Furthermore, the versatility of high-efficiency ERW tube mills cannot be overlooked. They are capable of producing a wide range of tube sizes and shapes, making them suitable for various applications. Whether it’s structural tubing for construction projects or high-strength tubes for energy transmission, these mills can be adapted to meet diverse production requirements. This flexibility allows manufacturers to cater to a broad customer base while reducing the need for multiple different machines.
The maintenance of high-efficiency ERW tube mills is also a critical aspect to consider. These machines are often designed with robustness and longevity in mind. With proper maintenance, the operational lifespan of these tube mills can be extended significantly, providing manufacturers with a favorable return on investment. Additionally, many modern mills come equipped with diagnostic tools that allow for real-time monitoring and predictive maintenance, thereby preventing unexpected downtimes and enhancing overall productivity.
In conclusion, the high-efficiency ERW tube mill represents a significant technological advancement in the manufacturing of welded tubes. Its ability to deliver precision, speed, and energy efficiency positions it as a critical asset for industries seeking to enhance their production capabilities and meet market demands. Manufacturers adopting this technology can expect to see improvements in operational efficiency, cost savings, and product quality. As technologies continue to evolve, high-efficiency ERW tube mills will undoubtedly play a pivotal role in shaping the future of manufacturing.