[Solid state HF welder customization service]Customized Solid State HF Welder Solutions: Tailoring High Frequency Welding Technology for Your Unique Industrial Needs
News 2024-9-1
In today’s competitive manufacturing environment, efficiency and precision are paramount, particularly in the realm of welding technologies. Solid state high-frequency (HF) welders have become increasingly popular due to their reliability, energy efficiency, and ability to provide clean and strong welds. However, not all welding applications are the same; different industries and projects demand varying specifications and capabilities. This is where solid state HF welder customization service comes into play, enabling manufacturers to optimize their welding processes according to their specific requirements.
Understanding Solid State HF Welding Technology
Solid state HF welding employs advanced electronic components, such as transistors and diodes, to generate high-frequency electrical currents. This technology utilizes electromagnetic energy to heat and bond materials, particularly in applications involving thermoplastic or thermoset materials. Unlike traditional welding methods, solid state HF welders are lightweight, compact, and capable of delivering more consistent results, making them ideal for industries that require precision and reliability.
The Importance of Customization
While standard solid state HF welders are effective for many applications, the complexity of manufacturing processes and materials calls for specialized solutions. Customization can encompass a range of parameters, including power output, frequency modulation, electrode design, and control systems. By offering tailored solutions, manufacturers can enhance their production lines, improve product quality, and significantly reduce operational costs.
For instance, an automotive parts manufacturer may require a solid state HF welder that operates at a specific frequency to ensure optimal bonding of plastic components. Conversely, a textiles company may need a machine that can handle a wider range of material thicknesses and shapes. Customization services make it possible to adapt the welder’s specifications to meet these diverse needs.
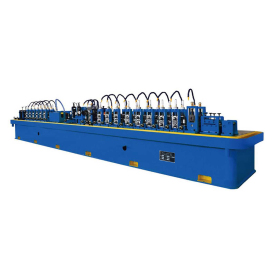
Customized Solid State HF Welder Solutions: Tailoring High Frequency Welding Technology for Your Unique Industrial Needs
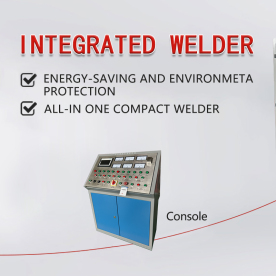
Customized Solid State HF Welder Solutions: Tailoring High Frequency Welding Technology for Your Unique Industrial Needs
1. **Power and Frequency Configuration**: Different applications may require different power outputs and frequency ranges. Custom engineers can fine-tune parameters to achieve the best performance for unique materials and welding techniques.
2. **Electrode Design**: The design of electrodes greatly influences the effectiveness of the welding process. Custom electrode designs can be developed to match the specific shapes and thicknesses of the materials being welded, ensuring optimal contact and heat transfer.
3. **Cooling Systems**: High-frequency welding generates considerable heat, making effective cooling essential for maintaining performance. Custom-designed cooling systems can be integrated to ensure the welder can operate continuously without overheating.
4. **Control Systems**: Advanced control systems can be implemented for more precise operation and monitoring. These systems can include automated feed mechanisms, real-time feedback loops, and programmable settings that accommodate multiple welding scenarios.
5. **Integration with Existing Processes**: It’s common for manufacturers to seek customization that allows for seamless integration with existing production lines. Custom welders can be designed to accommodate specific layouts or mechanical systems, ensuring operational continuity.
The Benefits of Custom Solid State HF Welders
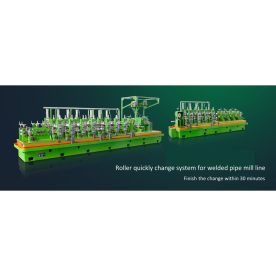
Customized Solid State HF Welder Solutions: Tailoring High Frequency Welding Technology for Your Unique Industrial Needs
- **Enhanced Efficiency**: Tailoring the welder minimizes downtime and streamlines the welding process, allowing for quicker production cycles. - **Improved Quality**: Customized settings can lead to superior welds, which are crucial in industries where safety and quality are non-negotiable. - **Cost-Effectiveness**: While there may be an initial investment in custom solutions, the long-term savings through reduced material waste and faster production times often outweigh the costs. - **Flexibility**: Manufacturers can adapt their operations to meet changing demands without needing to invest in entirely new equipment.
Partnering with Experts for Custom Solutions
To achieve the best results with solid state HF welder customization, partnering with experienced engineers and manufacturers is crucial. These experts can assess unique requirements, provide insights into the latest technology, and deliver solutions that align with business goals.
In conclusion, investing in a solid state HF welder customization service presents an opportunity for manufacturers to elevate their operational capabilities. By leveraging tailored technology, companies can ensure their welding processes are optimized for success in a demanding industrial landscape. Whether it's enhancing efficiency or improving product quality, customized solid state HF welders are pivotal for meeting the unique needs of every manufacturing environment.