[Induction heating]Exploring the Diverse Applications and Benefits of Induction Heating in Modern Manufacturing and Beyond
News 2024-9-1
****Induction heating is a process characterized by the generation of heat through electromagnetic induction, a method widely used in various industries and applications. As one of the most efficient and effective heating technologies available today, induction heating has transformed manufacturing processes, improved product quality, and enhanced efficiency in numerous applications. This article delves into the principle of induction heating, its diverse applications across different sectors, and the advantages it offers over traditional heating methods.
At its core, induction heating relies on the phenomenon of electromagnetic induction. When an alternating current passes through a coil, it generates a magnetic field. When a conductive material, typically a metal, is placed within this magnetic field, electrical currents are induced within the material, leading to the production of heat due to its electrical resistance. This process allows for selective heating of metals without direct contact, providing significant control over temperature and heating times.
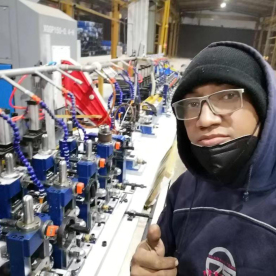
Exploring the Diverse Applications and Benefits of Induction Heating in Modern Manufacturing and Beyond
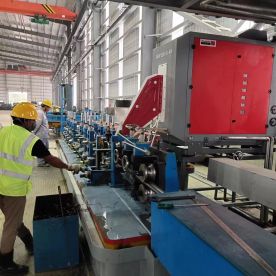
Exploring the Diverse Applications and Benefits of Induction Heating in Modern Manufacturing and Beyond
Another important application of induction heating is in the field of hardening and tempering. This method enables precise heat treatment of metal components, where specific areas can be heated to achieve desired hardness levels without affecting the entire part. As a result, manufacturers can produce intricate designs with enhanced durability, thereby extending the lifespan of the product.
Induction heating also finds its utility in the automotive sector, particularly for processes like brazing and soldering, where metal joints are required. By selectively heating the metal parts, induction heating provides better control than traditional methods, resulting in stronger and more reliable joints. Additionally, it minimizes the risk of damage to surrounding components, which is especially crucial in complex automotive assemblies.
Beyond metalworking, induction heating has made significant strides in the food processing industry. The technology has been explored for its potential in cooking and food safety applications. Induction cooktops, for instance, allow for faster and more efficient cooking by directly heating cookware instead of the burner, which in turn reduces energy consumption. This efficiency and precision are increasingly attractive to both commercial kitchens and home cooks alike, leading to its widespread adoption.

Exploring the Diverse Applications and Benefits of Induction Heating in Modern Manufacturing and Beyond
The benefits of induction heating extend beyond simple heating capabilities. One significant advantage is energy efficiency. Induction heating systems can reach target temperatures quickly and maintain them consistently, resulting in reduced energy consumption compared to conventional heating methods. This efficiency translates to lower energy costs, making induction heating an attractive option for manufacturers looking to cut expenses while maintaining stringent quality standards.
Moreover, induction heating produces less waste heat, contributing to a safer working environment. As the heat is generated within the material itself, the surrounding environment remains cooler, reducing the risk of heat-related injuries or equipment damage. This characteristic is particularly important in high-volume production settings where worker safety is a primary concern.
In conclusion, induction heating has established itself as a vital technology across a myriad of industries, from metalworking and automotive manufacturing to food processing and medical applications. With its myriad benefits, including energy efficiency, precision, and safety, it is poised to continue transforming manufacturing and heating processes for years to come. As technology advances, the potential for further innovations and applications of induction heating is boundless, making it an exciting area for ongoing exploration and development.