[Solid state HF welder customization service]Elevate Your Manufacturing Process with Custom Solid State HF Welder Customization Services Tailored to Your Unique Production Needs
News 2024-9-1
In today’s fast-paced manufacturing landscape, having the right tools for the job is more crucial than ever. One of the cornerstones of a productive manufacturing environment is an efficient welding system, especially when it comes to high-frequency (HF) welding. Enter solid-state HF welders—a game-changing technology that can significantly enhance the quality and speed of your welding processes. However, to fully leverage their capabilities, investing in Solid State HF Welder Customization Services can make all the difference.
Understanding Solid State HF Welding Technology
Solid-state HF welding utilizes advanced solid-state electronics to create high-frequency electromagnetic fields that heat and bond materials, typically thermoplastics. This innovative process has proven particularly effective for industries such as automotive, textiles, and packaging, where precise and strong joins are paramount. Solid-state welders are renowned for their energy efficiency, reduced maintenance costs, and the quality of welds they produce.
While off-the-shelf solid-state HF welders can meet general needs, they may not fully align with the specific requirements of your production line. This is where Solid State HF Welder Customization Services can be a game changer.
Why Customization Matters
1. **Tailored Performance:** Customized solid-state HF welders can be engineered to accommodate specific materials, shapes, and production speeds. Whether you need to weld a thicker material or require a unique electrode arrangement, a custom solution ensures that the welder's capabilities align perfectly with your manufacturing demands.
2. **Process Optimization:** By automating specific functions or incorporating unique features, customized welders can significantly streamline the welding process. This might include customized control interfaces, software integrations, or modular designs that allow quick adjustments based on changing project requirements.
3. **Enhanced Quality Control:** The quality of welds is critical for the longevity and reliability of the end product. Customized solid-state HF welders can integrate advanced quality control features such as real-time monitoring, which allows for immediate adjustments and ensures consistent weld strength and integrity.
4. **Scalability:** As your business grows, the demand for higher production rates may increase. Customizing your solid-state HF welder can facilitate scalability, allowing for easier upgrades and expansions, and thereby reducing the need for entirely new equipment as your requirements evolve.
5. **User-Friendly Operation:** User experience is an often-overlooked aspect of industrial machinery. Customization can provide a more intuitive interface and training features for operators, minimizing the learning curve and reducing chances for operator error.
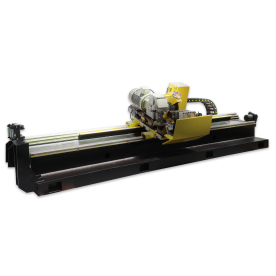
Elevate Your Manufacturing Process with Custom Solid State HF Welder Customization Services Tailored to Your Unique Production Needs
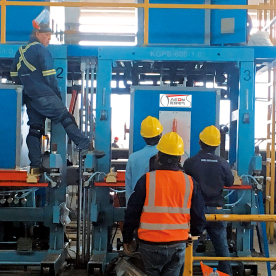
Elevate Your Manufacturing Process with Custom Solid State HF Welder Customization Services Tailored to Your Unique Production Needs
Investing in Solid State HF Welder Customization Services will generally involve several stages:
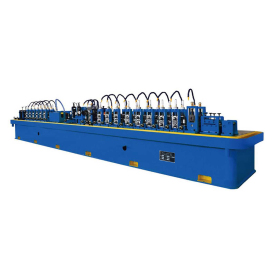
Elevate Your Manufacturing Process with Custom Solid State HF Welder Customization Services Tailored to Your Unique Production Needs
2. **Design and Engineering:** After identifying your needs, engineers will work on designing a customized welder that incorporates the required modifications and features. This phase is critical as it incorporates feedback from your operational team to ensure the final product matches user expectations.
3. **Manufacturing and Testing:** Upon finalizing the design, the welding machine will undergo manufacturing, followed by rigorous testing to validate performance against your specific requirements. This phase ensures that any potential issues are identified and rectified before installation.
4. **Installation and Training:** After successful testing, the customized welder will be installed at your facility. Comprehensive training sessions will be provided for your operators, ensuring they are comfortable and proficient in using the new equipment.
5. **Ongoing Support:** Continued support and maintenance are vital for any industrial machinery. Reliable customization service providers will offer ongoing technical support, ensuring your welder operates efficiently and remains aligned with your growing business needs.
Conclusion
In summary, investing in Solid State HF Welder Customization Services could be the key to unlocking the full potential of your manufacturing processes. By tailoring the welder to your specific operational requirements, you can achieve optimized efficiency, superior weld quality, and greater scalability. The return on investment is often pronounced, leading to increased productivity, reduced downtime, and ultimately, superior products. As you explore enhancement options for your welding processes, consider the substantial benefits that customized solid-state HF welding solutions can bring to your operation.