[Roller for tube mill]Exploring the Role of Rollers in Tube Mill Operations: Enhancing Efficiency and Quality in Metal Forming Processes
News 2024-8-31
****The manufacturing and processing of metal tubes have long been pivotal in various industries, including construction, automotive, aerospace, and energy. At the heart of this process lies an essential component: the roller for the tube mill. These rollers play a crucial role in shaping, forming, and finishing metal tubes, and understanding their significance can uncover insights into the efficiency and quality of tube production.
**What is a Tube Mill?**
A tube mill is a type of equipment that continuously forms metal strips or sheets into tubes or pipes. The tube manufacturing process typically involves heating the metal input—often steel—and then feeding it through a series of rollers. These rollers shape the metal into a tubular form, which is then further processed to meet specific standards. Tube mills come in various designs and capabilities, often tailored for specific applications, including welded and seamless tubes.
**The Importance of Rollers in Tube Mills**
Rollers in a tube mill are engineered specifically to perform a range of functions critical to the tube manufacturing process. Their roles include shaping the metal, reducing thickness, smoothing weld seams, and providing the necessary surface finish. They are integral to managing the flow and deformation of the metal as it passes through the mill, ensuring that the final product meets precise dimensional and structural requirements.
**Types of Rollers Used in Tube Mills**
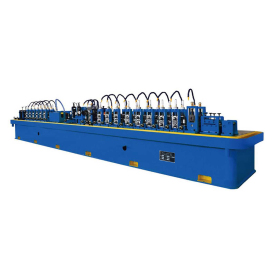
Exploring the Role of Rollers in Tube Mill Operations: Enhancing Efficiency and Quality in Metal Forming Processes
2. **Welding Rollers:** After forming the tube, the edges are brought together and welded. Welding rollers ensure that the weld is uniform and applies consistent pressure during the welding process, which is crucial for the overall integrity and strength of the tube.
3. **Sizing Rollers:** Once the tube is formed and welded, sizing rollers are used to ensure that the tube reaches the correct diameter and wall thickness. This step is vital for maintaining the specified tolerances required for various applications.
4. **Finishing Rollers:** These rollers are used to give the final tube its surface finish and to refine the dimensional accuracy. They contribute to the aesthetic qualities of the product as well as its mechanical characteristics.
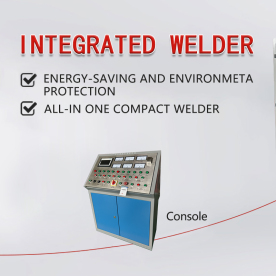
Exploring the Role of Rollers in Tube Mill Operations: Enhancing Efficiency and Quality in Metal Forming Processes
Effective roller design and maintenance can significantly influence tube mill performance. Each set of rollers may be optimized based on factors such as the type of metal being processed, the desired tube specifications, and the production volume.
1. **Material Selection for Rollers:** The materials used to manufacture rollers can impact their longevity and performance. High-quality steels and alloy materials are often selected for their durability and resistance to wear and deformation.
2. **Precision Engineering:** Rollers must be engineered to exact specifications to ensure that they perform consistently. Variations in roller dimensions can lead to defects and non-compliance with product standards.
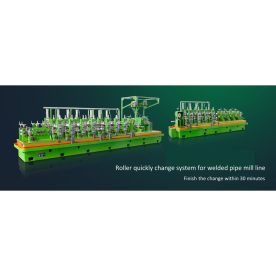
Exploring the Role of Rollers in Tube Mill Operations: Enhancing Efficiency and Quality in Metal Forming Processes
4. **Advancements in Roller Technology:** Innovations in roller design, such as surface coatings and heat treatments, have enhanced the performance of rollers in tube mills. Such advancements can lead to greater operational efficiency, reduced downtime, and improved product quality.
**Conclusion**
The roller for the tube mill is an indispensable component in the realm of metal tube manufacturing. Its effects ripple through the entire production process, influencing material flow, product quality, and overall operational efficiency. Understanding the technology and methodology behind tube mill rollers not only highlights their importance but also unveils opportunities for enhancement in production practices. As industries continue to evolve and demands for high-quality tubing increase, the role of rollers in tube mills will remain a focal point of innovation and efficiency optimization. The collaboration between technology and engineering in this field holds the promise of advancing tube mill operations well into the future.