[Tube mill production line]An In-Depth Look at Tube Mill Production Line: Enhancing Efficiency and Quality in Metal Pipe Manufacturing
News 2024-8-30
The tube mill production line plays a critical role in the manufacturing industry, particularly in producing high-quality metal pipes and tubes utilized in a plethora of applications, from industrial machinery to construction projects. Given the growing demand for durable and reliable tubing solutions, understanding the intricacies of a tube mill production line is essential for manufacturers looking to optimize production efficiency and product quality. This article delves into the various components, processes, and technological advancements associated with tube mill production lines.
Understanding Tube Mill Production Lines
At its core, a tube mill production line is a sophisticated assembly system designed for the continuous manufacturing of tubular products. The process typically begins with a flat steel strip, which is fed into the mill, where it undergoes a series of forming, welding, and finishing procedures to create a seamless and high-quality pipe.
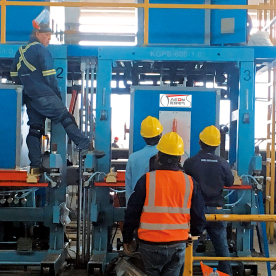
An In-Depth Look at Tube Mill Production Line: Enhancing Efficiency and Quality in Metal Pipe Manufacturing
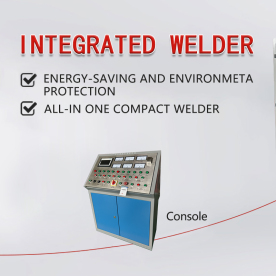
An In-Depth Look at Tube Mill Production Line: Enhancing Efficiency and Quality in Metal Pipe Manufacturing
2. **Uncoiling and Leveling**: The steel coils are uncoiled and flattened using leveling equipment to prepare for further processing. This ensures that the material is flat and uniform, which is crucial for the subsequent forming processes.
3. **Forming**: The flat steel strips are formed into a cylindrical shape through a series of rollers in the mill. Each set of rollers shapes the strip gradually, ensuring uniformity and precision in diameter. Depending on the design and requirements, the pipe can be manufactured with different wall thicknesses and diameters.
4. **Welding**: As the tube is formed, edges of the steel strip are brought together and welded using various methods, including high-frequency induction welding (HFIW) or submerged arc welding (SAW). This step is critical, as it determines the structural integrity of the pipe. Advanced welding technologies ensure minimal heat distortion and a strong joint.
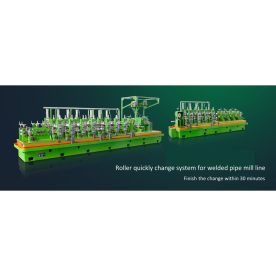
An In-Depth Look at Tube Mill Production Line: Enhancing Efficiency and Quality in Metal Pipe Manufacturing
6. **Quality Control**: Throughout the tube mill production line, quality control measures are paramount. Techniques such as non-destructive testing (NDT) and dimensional inspections ensure that the final product adheres to industry standards and specifications. Automated systems keep track of any defects ensuring high-quality output.
7. **Cutting and Packaging**: Once the tubing is manufactured and inspected, it is cut to the desired lengths. The finished products are then packaged carefully for transportation, often involving protective measures to prevent damage during shipping.
Technological Advancements in Tube Mill Production Lines
In recent years, the tube mill production line has seen significant advancements in technology, enhancing both efficiency and product quality. Automation plays a pivotal role, with automated systems designed to monitor and control various aspects of the production process. This not only speeds up operations but also minimizes human error.
Moreover, advancements in welding technology, such as laser welding, offer improved precision and heat management, resulting in stronger and more reliable welds. Additionally, the implementation of Industry 4.0 concepts, including the Internet of Things (IoT) and data analytics, allows manufacturers to collect and analyze data in real-time, leading to better decision-making and predictive maintenance.
Conclusion
The tube mill production line is an essential aspect of modern manufacturing, particularly in sectors that require precise and durable metal tubes and pipes. By understanding the processes involved and the technological advancements available, manufacturers can significantly enhance efficiency, reduce costs, and improve quality standards. As industries continue to innovate and grow, the importance of a well-designed and efficiently operated tube mill production line will only increase, positioning it as a cornerstone of the manufacturing process in the years to come.