[Automatic high frequency welder]Understanding the Benefits and Applications of Automatic High Frequency Welders in Modern Manufacturing Processes
News 2024-8-30
In the realm of modern manufacturing, efficient and precise welding techniques are pivotal for producing high-quality products. Among these techniques, the automatic high frequency welder stands out as a revolutionary tool that dramatically enhances productivity and quality in various welding applications. This article delves into the working principles, benefits, and diverse applications of automatic high frequency welders, showcasing why they have become an integral component in many manufacturing processes.
The Mechanics of Automatic High Frequency Welders
Automatic high frequency welding is a process wherein a high-frequency electromagnetic field is employed to join materials, particularly thermoplastics and metals. The fundamental operation involves generating high-frequency currents that are transmitted through welding electrodes. When two materials are brought into contact within this field, localized heating occurs due to the resistance of the materials, resulting in a strong weld upon cooling.
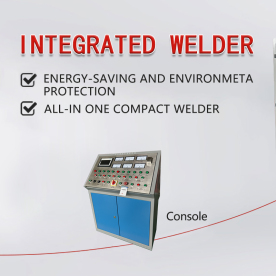
Understanding the Benefits and Applications of Automatic High Frequency Welders in Modern Manufacturing Processes
Key Benefits of Automatic High Frequency Welders
1. **Increased Efficiency**: One of the most significant advantages of using an automatic high frequency welder is the enhanced efficiency of the welding process. The automation enables faster operation speeds and reduced cycle times compared to traditional welding methods. This is especially beneficial in high-volume production environments, where time is of the essence.
2. **Quality Control**: Automatic high frequency welders incorporate advanced monitoring and control systems that ensure the welding parameters remain within specified limits. This consistent monitoring results in higher quality welds and less variability in the finished product. In industries where precision is critical, such as electronics and automotive manufacturing, this attribute is invaluable.
3. **Versatility**: These welders are extremely versatile and can be used for a variety of materials including but not limited to metals, plastics, and composites. This adaptability allows manufacturers to integrate automatic high frequency welders into multiple production lines, making them a worthwhile investment.
4. **Cost-Effectiveness**: Although the initial investment in automatic high frequency welding equipment may be higher than traditional welding systems, the long-term savings can be significant. The combination of increased productivity, lower labor costs, and reduced material waste contributes to an overall decrease in manufacturing expenses.
5. **Reduced Heat Affected Zone**: Unlike traditional welding methods that can result in a large heat-affected zone, automatic high frequency welding concentrates the heat on the welding interface. This means less thermal distortion of the surrounding material and minimized alterations in material properties, which is crucial for maintaining the integrity of components in sensitive applications.
Applications of Automatic High Frequency Welders
The applications for automatic high frequency welders span a wide range of industries.
- **Automotive Industry**: In automotive manufacturing, these welders are used for joining metal components, creating strong and lightweight structures that enhance overall vehicle performance.
- **Electronics Manufacturing**: Automatic high frequency welders play a crucial role in the electronics sector, where they are employed to connect components with precision while minimizing damage to sensitive parts.
- **Textile and Packaging Industries**: These welders are also widely used in the textile and packaging industries for joining mesh fabrics, laminating materials, and welding flexible packaging.
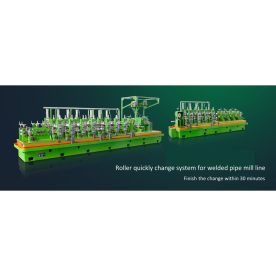
Understanding the Benefits and Applications of Automatic High Frequency Welders in Modern Manufacturing Processes
Conclusion
