[High frequency welder manufacturer]An In-Depth Look at High Frequency Welder Manufacturers: Quality, Innovation, and Market Trends in 2023
News 2024-8-30
****In the realm of industrial manufacturing, welding remains one of the most critical processes for joining materials, particularly metals. Among the various welding techniques, high frequency welding has gained significant traction due to its efficiency and quality. As a result, the demand for high frequency welder manufacturers is on an upward trajectory. This article delves into the world of high frequency welding, explores key manufacturers, and highlights the market trends that shape this essential industry.
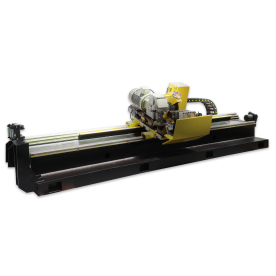
An In-Depth Look at High Frequency Welder Manufacturers: Quality, Innovation, and Market Trends in 2023
High frequency welding, also known as high frequency induction (HFI) welding, involves the use of high-frequency electrical currents to heat materials and join them together. The process is particularly popular in the production of pipes, tubes, and other cylindrical materials. Unlike conventional welding methods, high frequency welding operates at higher frequencies, resulting in quicker heating, reduced cycle times, and stronger welds. This method allows for superior control over the welding process, which is critical for industries where precision is paramount.
Importance of High Frequency Welder Manufacturers
The role of high frequency welder manufacturers cannot be overstated. They are responsible for producing state-of-the-art equipment that enhances the efficiency, quality, and reliability of high frequency welding processes. Manufacturers play a crucial part in implementing new technologies that improve the welding experience, reduce energy consumption, and minimize operational costs. Additionally, these manufacturers support various industries, ranging from automotive and aerospace to construction and energy, making their contributions vital to economic growth.
Key Manufacturers in the High Frequency Welding Industry
1. **Miller Electric**: A prominent player in the welding equipment market, Miller Electric has a solid reputation for producing high-quality welding machines. Their high frequency welders are known for their innovative designs and user-friendly interfaces, making them a popular choice for industrial applications.
2. **Lincoln Electric**: As one of the oldest and most notable manufacturers in the welding industry, Lincoln Electric offers a comprehensive range of welding products. Their high frequency welders incorporate advanced technology that ensures precision and efficiency in various welding applications.
3. **ESAB**: Renowned for its commitment to innovation, ESAB manufactures high frequency welding equipment tailored for diverse industries. Their welders are equipped with advanced features, ensuring maximum reliability and performance under challenging conditions.
4. **AMADA WELD TECH**: AMADA WELD TECH specializes in welding solutions that focus on precision and efficiency. Their high frequency welder models are widely used in the electronics and automotive sectors, where quality is non-negotiable.
5. **RMD Engineering**: Known for developing high frequency welding machines that cater to specific industrial needs, RMD Engineering focuses on customization and advanced engineering solutions to meet distinctive welding challenges.
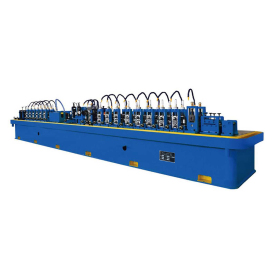
An In-Depth Look at High Frequency Welder Manufacturers: Quality, Innovation, and Market Trends in 2023
As we move further into 2023, several trends are shaping the landscape of high frequency welding and manufacturing:
- **Automation and Industry 4.0**: The integration of smart technologies in manufacturing continues to rise. High frequency welder manufacturers are increasingly incorporating automation and artificial intelligence into their equipment, resulting in enhanced precision, reduced labor costs, and improved productivity.
- **Sustainability**: Growing awareness of environmental issues is prompting manufacturers to develop more energy-efficient machines that reduce waste and minimize the carbon footprint. High frequency welding presents itself as a more sustainable option due to lower energy consumption compared to traditional welding methods.
- **Customization**: As industries become more specialized, the need for customized welding solutions has increased. Manufacturers are responding by offering tailor-made equipment designed to meet specific client needs, including unique power requirements, material types, and production processes.
- **Training and Support**: With the technological advancements in high frequency welding, manufacturers are recognizing the importance of comprehensive training and support for their clients. Offering robust training programs ensures that operators can effectively use the latest equipment, maximizing productivity and minimizing errors.
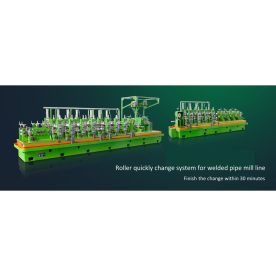
An In-Depth Look at High Frequency Welder Manufacturers: Quality, Innovation, and Market Trends in 2023
The high frequency welder manufacturers play a pivotal role in advancing welding technologies and supporting various industries. As we continue to witness rapid changes in manufacturing techniques and market demands, these manufacturers are poised to lead the way through innovation and responsiveness. The future of high frequency welding is bright, marked by automation, sustainability, and customization, ensuring that industries continue to thrive amid evolving challenges and opportunities.