[High frequency welder for plastic]Innovative Solutions with High Frequency Welder for Plastic: Revolutionizing Manufacturing Processes in Various Industries
News 2024-8-30
In the modern manufacturing landscape, the need for efficient, reliable, and precise joining techniques has never been more paramount. With the rise of plastics in various applications, especially in consumer goods, automotive, medical, and electronic industries, the high frequency welder for plastic has emerged as a game-changer in the welding and bonding sector. This advanced technology not only enhances production efficiency but also improves the quality and durability of plastic components.
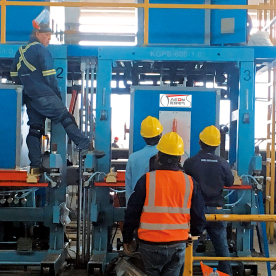
Innovative Solutions with High Frequency Welder for Plastic: Revolutionizing Manufacturing Processes in Various Industries
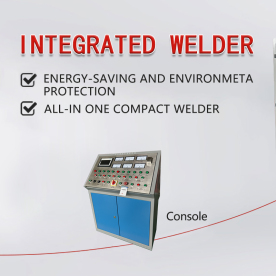
Innovative Solutions with High Frequency Welder for Plastic: Revolutionizing Manufacturing Processes in Various Industries
High frequency welding technology has vast applications across various sectors. In the automotive industry, for example, it is used to manufacture components such as dashboards, door panels, and airbag casings. These parts require not only strength but also precision, as the components need to fit together seamlessly to ensure safety and functionality. The high frequency welder allows manufacturers to achieve tight tolerances, which is essential in the highly regulated automotive environment.
In the electronic sector, the technology is widely implemented in producing components like mobile device casings, power cords, and connectors. The rapid welding process minimizes production time, enabling manufacturers to respond quickly to market demands. Additionally, the efficacy of high frequency welding in creating waterproof and dustproof seals makes it ideal for electronic applications, where exposure to the elements can lead to malfunction.
Moreover, the packaging industry greatly benefits from high frequency welders. The ability to create strong, leak-proof seals for plastic packaging ensures the integrity of food and pharmaceuticals during storage and transportation. Consumers increasingly demand not just durability but also eco-friendliness in product packaging. The high frequency welder for plastic, by eliminating the need for solvents, contributes to more sustainable practices in manufacturing.
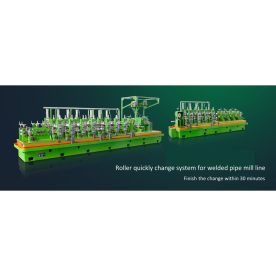
Innovative Solutions with High Frequency Welder for Plastic: Revolutionizing Manufacturing Processes in Various Industries
However, implementing high frequency welding comes with its own set of challenges. Material selection is crucial, as not all plastics respond equally to the process. Additionally, maintaining equipment and ensuring consistent machine performance is vital to avoid production downtimes. Businesses may need to invest in high-quality machinery and regular maintenance to maximize the returns on their investment.
Furthermore, as industries evolve, so does the technology surrounding high frequency welding. Innovations in software and automation are paving the way for more accurate and efficient welding processes. Manufacturers are increasingly looking to integrate smart technology into their operations to monitor and control welding parameters in real-time, ensuring optimal performance and product quality.
In conclusion, the high frequency welder for plastic represents a revolutionary advancement in manufacturing technology. Its ability to create strong, precise, and environmentally friendly welds makes it a vital tool across various industries. As technology continues to evolve and improve, companies utilizing high frequency welders can enhance their production processes, reduce costs, and meet the increasingly stringent quality demands of the modern market. Embracing this innovative solution is not just an opportunity; it is a necessity for those looking to remain competitive in the rapidly changing manufacturing landscape.