[Precision induction heating equipment]Understanding the Benefits and Applications of Precision Induction Heating Equipment in Modern Manufacturing Processes
News 2024-8-28
In today's fast-paced manufacturing world, precision is the backbone of efficiency and quality. With advancements in technology driving the need for enhanced performance, industries are increasingly turning to precision induction heating equipment. This innovative heating method offers numerous advantages over traditional heating techniques. By understanding what precision induction heating equipment is and its myriad applications, manufacturers can leverage its benefits to improve their processes.
What is Precision Induction Heating Equipment?
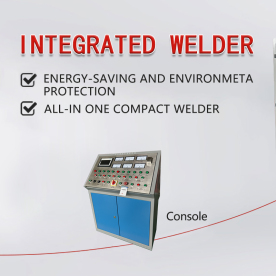
Understanding the Benefits and Applications of Precision Induction Heating Equipment in Modern Manufacturing Processes
The precision aspect comes from the equipment's ability to control the heating process meticulously. The temperature can be adjusted with high accuracy and monitored in real-time, allowing for specific heating profiles tailored to different materials and applications. This capability makes precision induction heating equipment particularly appealing for industries that require strict adherence to temperature specifications.
Key Benefits of Precision Induction Heating Equipment
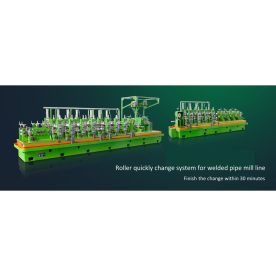
Understanding the Benefits and Applications of Precision Induction Heating Equipment in Modern Manufacturing Processes
2. **Fast Heating Speeds**: Induction heating systems can reach operational temperatures in a fraction of the time taken by conventional heating methods. This rapid heating allows manufacturers to increase their production rates and reduce cycle times, thereby optimizing throughput.
3. **Uniform Heating**: Precision induction heating ensures uniform temperature distribution across the heating volume. This characteristic is crucial for applications like hardening, soldering, and brazing, where uneven heating can lead to defects and structural weaknesses in the finished product.
4. **Safety and Control**: The controlled environment of induction heating minimizes the risks associated with open flames or extensive hot surfaces. It also offers a more controlled and safer process since the equipment can quickly shut off when a target temperature is reached or when materials are removed from the heating zone.
5. **Reduced Waste**: The precise control of temperature and heating times helps to maintain material integrity and reduce wastage. In industries where rare or expensive materials are used, such as aerospace or medical manufacturing, this benefit can have significant financial implications.

Understanding the Benefits and Applications of Precision Induction Heating Equipment in Modern Manufacturing Processes
Precision induction heating equipment finds application across various sectors, including:
- **Metal Hardening**: Induction hardening is a common process in which steel parts are heated and then rapidly cooled to increase hardness. This method is crucial in manufacturing components subject to wear, such as gears and axles.
- **Brazing and Soldering**: The uniform heating characteristics make induction heating ideal for brazing and soldering applications, allowing for strong joints in various assemblies without damaging surrounding materials.
- **Melting and Casting**: In foundries, induction heating is employed to melt metals for casting. Its efficiency and ability to maintain consistent temperatures ensure high-quality metal production.
- **Heat Treatment**: Industries utilize induction heating for heat treatment processes to alter material properties, including tensile strength, ductility, and toughness, to meet specific end-use requirements.
- **Plastic Welding**: Some designers are using precision induction heating in plastic welding processes, where careful control of the heating profiles is vital to ensure proper bonding without damaging components.
Conclusion
Precision induction heating equipment represents a leap forward in manufacturing technology, offering unparalleled efficiency, safety, and control. As industries strive for greater accuracy in production, induction heating continues to gain traction as a preferred method. By investing in this advanced technology, manufacturers can not only improve their process efficiency but also enhance product quality, reduce costs, and stay competitive in a rapidly evolving marketplace. Embracing precision induction heating equipment is indeed a strategic move toward a smarter, more efficient future in manufacturing.