[Customized Mould for Tube Mill Components]The Importance of Customized Mould for Tube Mill Components in Enhancing Productivity and Efficiency in Manufacturing
News 2024-8-28
****In the modern manufacturing landscape, optimizing production processes while ensuring high-quality output is paramount. One pivotal component that contributes to achieving these goals is the use of customized moulds for tube mill components. These moulds are designed specifically for the unique requirements of each production run, allowing manufacturers to streamline operations, reduce waste, and ultimately enhance their competitive edge. This article delves into the significance of using customized moulds in tube mill production, exploring their benefits, applications, and impact on overall manufacturing efficiency.
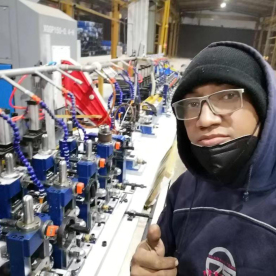
The Importance of Customized Mould for Tube Mill Components in Enhancing Productivity and Efficiency in Manufacturing
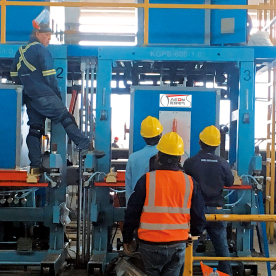
The Importance of Customized Mould for Tube Mill Components in Enhancing Productivity and Efficiency in Manufacturing
Why Customized Moulds?
The use of standardized moulds may work for some production runs; however, there are several compelling reasons to invest in customized moulds for tube mill components:
1. **Precision and Quality**: Customized moulds allow for precise engineering that meets specific production demands. This precision results in higher quality components with fewer defects, reducing the need for rework or scrap.
2. **Enhanced Production Efficiency**: Tailoring moulds to fit specific machinery and production processes can dramatically decrease setup times and increase machine output. Customized moulds can be designed to facilitate smoother operations, ensuring that the tube mill can run at optimal speeds without interruptions.
3. **Adaptability**: The manufacturing landscape is continually evolving, with new materials and designs being developed. Customized moulds can be easily modified or redesigned to accommodate these changes, allowing manufacturers to stay competitive in a dynamic market.
4. **Cost-Effectiveness**: While the initial investment in customized moulds may be higher than standardized options, the long-term savings can be significant. Fewer defects, reduced material waste, and less downtime all contribute to lower overall production costs.
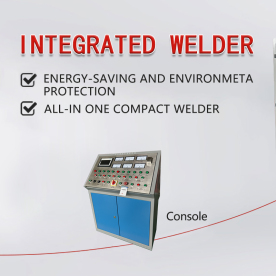
The Importance of Customized Mould for Tube Mill Components in Enhancing Productivity and Efficiency in Manufacturing
Applications in Various Industries
Customized moulds for tube mill components are utilized across various industries:
- **Automotive Industry**: In the automotive sector, tube components are critical for frameworks and fuel delivery systems. Customized moulds ensure that these components meet the stringent safety and performance standards required in this highly regulated field.
- **Construction**: The construction industry relies heavily on tube products such as scaffolding and piping. Customized moulds help in producing these components with the right dimensions and strength, which are crucial for structural integrity.
- **Energy Sector**: Tubes used in pipelines and other energy infrastructure must withstand high pressures and temperatures. Customized moulds can be engineered specifically for the rigors of these applications, ensuring reliability and longevity.
Conclusion
The integration of customized moulds for tube mill components reflects a significant step forward in manufacturing efficiency and effectiveness. As industries continue to demand higher quality, adaptability, and lower costs, customized moulds provide a solution that meets these challenges head-on. Manufacturers who invest in tailored mould solutions can expect to see improvements not only in production lines but across their entire operations. This commitment to precision and quality enables businesses to thrive in an increasingly competitive marketplace, securing their future and ensuring they do not merely keep pace with industry trends, but lead them.